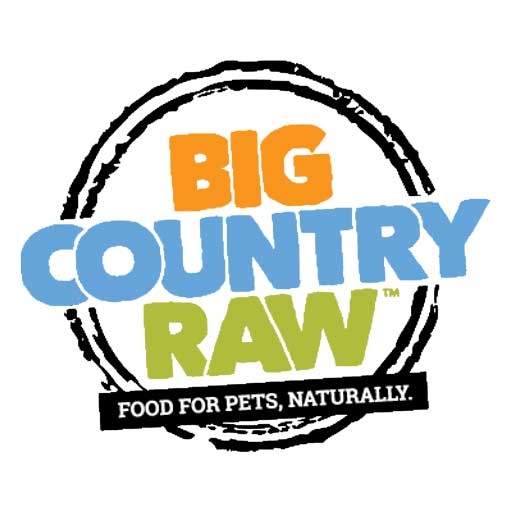
Big Country Raw, a pet food manufacturer, selling 100% through DTC channels.
Industry Food and Beverage, DTC
Services Digital Transformation Roadmap
Business Process Re-engineering
Enterprise Architecture Development
Vendor Selection
Software Contract Negotiation
Project and Change Management
Requirements Management
Master Data Governance Framework
Data Conversion
Platforms Acumatica
WooCommerce
QuickBooks
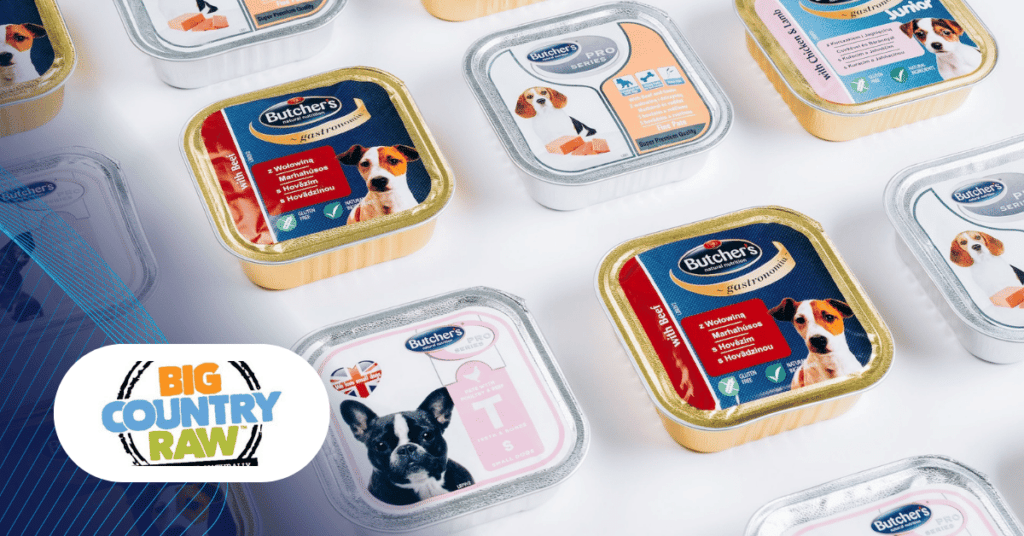
Big Country Raw Case Study
Digital Transformation Change and Project Management
Learn how Big Country Raw managed the change and transformation despite their limited budget for ERP implementation and eCommerce integration.
Problem Despite working with other selection firms, they struggled with how ERP would fit with their business.
Even though they used over 55 plugins over WooCommerce, they still struggled with basic ERP scenarios such as 3-way match.
With limited expertise in enterprise applications, they struggled to prioritize whether they should move first to Magento or to an ERP.
Given the challenges such as in-house logistics, their business model was unique, unlike other traditional retailers and food and beverage manufacturers.
Growing out of QuickBooks, they needed substantial help with data conversion, including creating BOMs and formulas from scratch. They never had them finalized.
The quick growth resulted in an ever-evolving business model with several warehouses being planned at the same time as as-is and to-be states were being finalized.
Solution As-is and To-be process models built
Process reengineering recommendations
New inventory reconciliation models
Superior material movement flow
Business, process, information, and system architecture built
Change management plan formalized
Source of authority and system interaction flow built
Data cleansing recommendations provided
New BOMs and formulas aligned with Acumatica’s data model created
Outcome The system footprint consolidated by 70%
Alignment of as-is and to-be process models for executive teams
The opportunity costs for internal teams were reduced by 70%
ERP implementation costs less than 20% of the industry average
Total potential savings of over $200K through vendor discounts
The duplicate data entry efforts reduced by 40% through integrated processes and systems
The inventory and matching accuracy increased by 50% through tight financial control
Superior insights into the financials and expenses to build scalable operational capacity
Discover Related Customer Stories
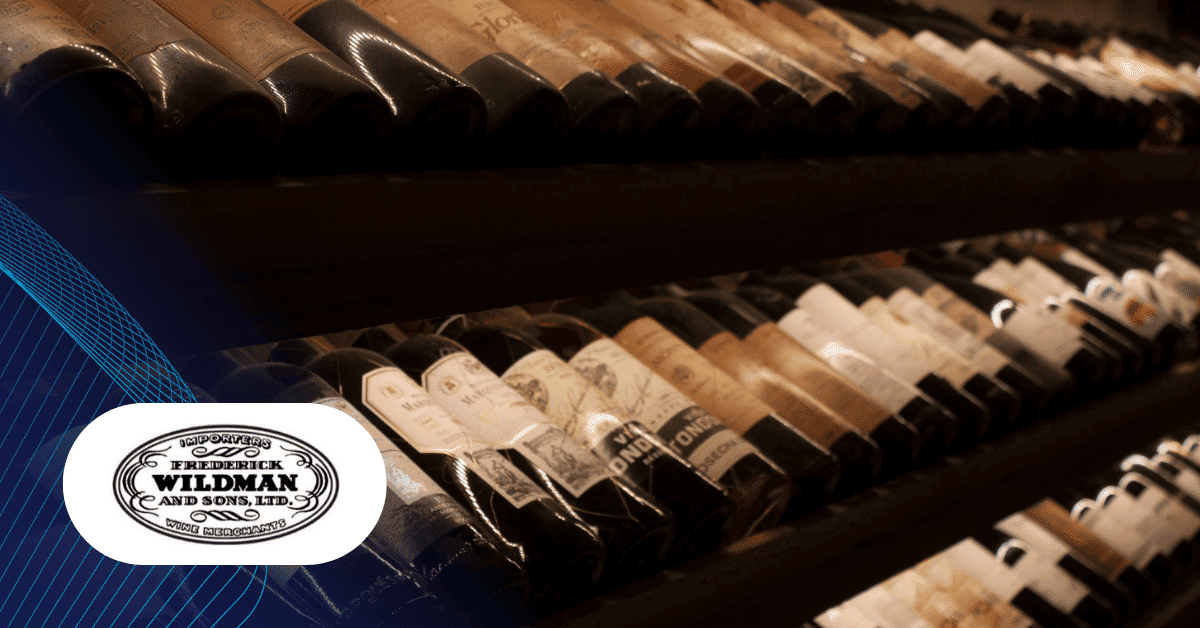
ERP Implementation Failure Recovery
Download the ERP implementation failure recovery failure case study and learn how Frederick Wildman struggled with Microsoft Dynamics 365 ERP implementation failure even after spending over $5M and what options they had for recovery.
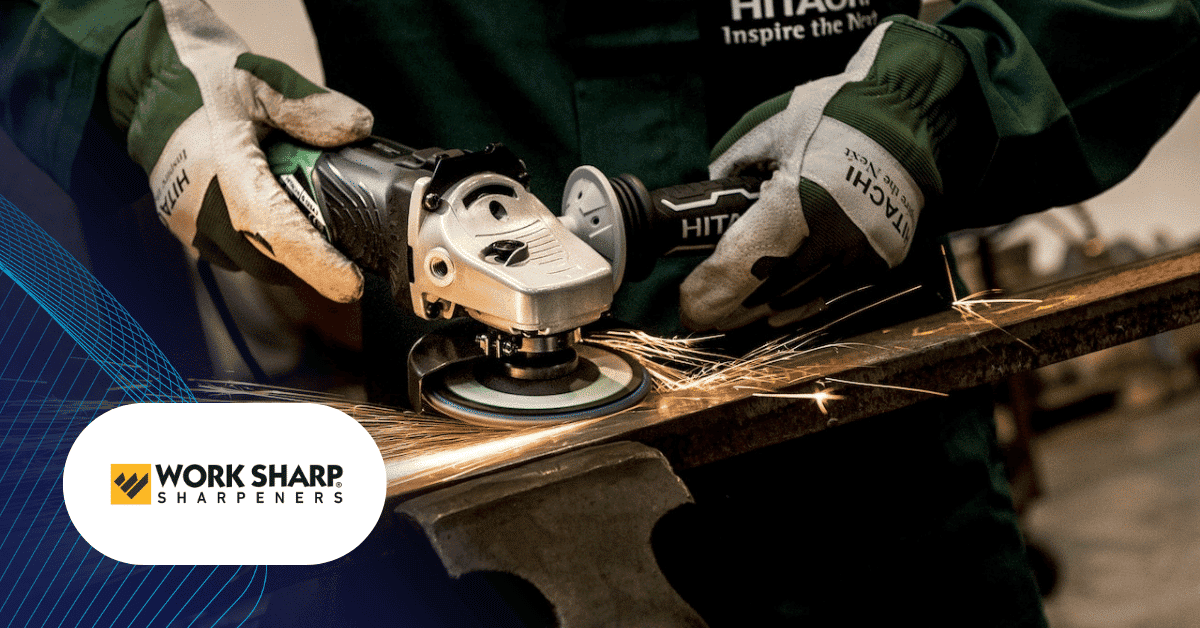
ERP Optimization and Integration Architecture Development
Download the ERP optimization and integration architecture development case study and learn how Work Sharp fixed their broken ERP implementation that caused customer service issues and improved Supply Chain planning.

Mergers and Acquisitions ERP Integration Failure Rescue
Download the mergers and acquisitions ERP integration failure Case Study and learn how Pride Sports struggled with Supply Chain and inventory allocation issues, as well as operational disruptions due to poorly planned M&A integration and ERP transformation project.