Last Updated on November 27, 2023 by Sam Gupta
In this episode, we have our guest Amanda Schleede, who discusses how manufacturers and retailers can better manage disruptions associated with COVID spread. She also provides insight into reporting requirements related to COVID. Finally, we have had a chance to describe how contact tracing works and how it can help manufacturers understand and analyze trends.
Chapter Markers
- [0:20] Intro
- [2:30] Personal journey and current focus
- [4:47] What is contact tracing?
- [9:25] Industries relevant for contact tracing
- [12:25] Technology architecture for contact tracing
- [15:50] The limitations of Bluetooth technology
- [22:13] Data points available through contact tracing
- [26:33] The financial implications due to the lack of contact tracing
- [30:11] How manufacturers can prevent COVID in their facility?
- [33:12] Closing thoughts
- [35:45] Outro
Key Takeaways
- If somebody can prove that they contracted COVID from their workplace, it is actually considered a workman’s comp claim. And so there are situations where we’ve seen them in the news where, employees are suing their employers because they got COVID on it, and their employer site and so on.
- The downstream effects of showing your employees that you care about their health and safety, that you’re putting risk mitigation in place. So from your insurance carriers to your workman’s comp carriers, to your lawyers, all of this, you’re really showing that you’re doing something to mitigate the risk of somebody coming in whether they know it or not, being COVID positive, and, infecting your entire employee pool.
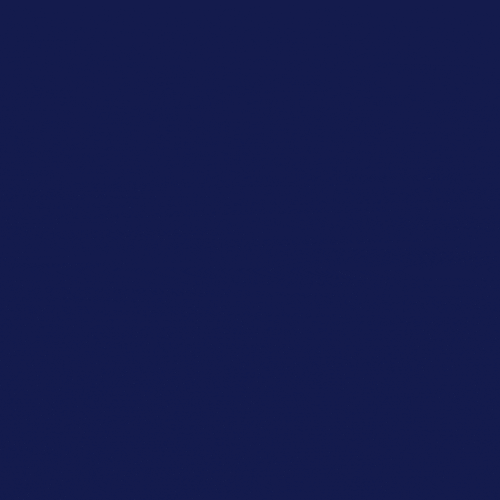
Subscribe and Review
Apple | Spotify | Stitcher | Google Podcasts | Deezer | Player FM | Castbox
About Amanda
With over twenty-five years of healthcare-focused experience within the management consulting, service, and venture capital worlds, Amanda has honed her skills to get the job done. Her previous experience working for multiple entrepreneurial-based organizations provides her with the experience to grow Vital Circle. She can anticipate client needs and the road ahead. Her extensive experience focused on organizational design and needs assessment, provides Vital Circle clients with an inside perspective in developing and implementing a full health protocol playbook for their organization.
Resources
- Connect with Amanda
Full Transcript
Amanda Schleede 0:00
Then that way, an organization can say okay, instead of shutting down an entire plant or an entire line in a manufacturing situation, we only have to identify four or five, six people who we need to say, hey, we need to put you on Cobra pay, or we need to have you work from home. And so, really, what it’s doing is creating a situation where there aren’t these downstream effects.
Intro 0:20
Growing a business requires a holistic approach that extends beyond sales and marketing. This approach needs alignment among people, processes, and technologies. So if you’re a business owner, operations, or finance leader looking to learn growth strategies from your peers and competitors, you’re tuned into the right podcast. Welcome to the WBS podcast, where scalable growth using business systems is our number one priority. Now, here is your host, Sam Gupta.
Sam Gupta 0:56
Hey everyone, welcome back to another episode of the WBS podcast. I’m Sam Gupta, your host and principal consultant at digital transformation consulting firm ElevatIQ.
COVID has been harsh on everyone. But if you have a COVID incident in your facility, not only will there be significant disruption with your operations, but there may also be additional overhead of reporting for your already overworked HR department. What can facilities do to manage their facilities better while taking care of their employees’ health?
In today’s episode, we have our guests Amanda Schleede, who discusses how manufacturers and retailers can better manage disruptions associated with COVID spread. She also provides insight into reporting requirements related to COVID. Finally, she has had a chance to describe how contact tracing works and how it can help manufacturers understand and analyze trends. Let me introduce Amanda to you.
Sam Gupta 1:50
With over 25 years of healthcare-focused experience within the management consulting service and venture capital worlds. Amanda has the skills to get the job done. Her previous experience working for multiple entrepreneurial-based organizations provides her with the experience to grow Vital Circle, anticipate client needs and the road ahead. Her extensive experience focused on organizational design and needs assessment provides vital circle clients with an insight perspective and developing and implementing a full health protocol playbook for the organization. With that, let’s get to the conversation. Welcome to the show, Amanda.
Amanda Schleede 2:28
Thank you, Sam. Thanks for having me.
Sam Gupta 2:30
Just to kick things off, do you wanna start with your personal story and your current focus these days?
Amanda Schleede 2:36
Sure, so my name is Amanda Schleede. I am the CEO of Vital Circle. I have started Vital Circle with a friend of mine who is actually the Chief Nursing Informatics Officer at Atrium Health in North Carolina. Prior to starting Vital Circle, I owned my own consulting firm, which focuses on helping organizations identify pain points within the organization, really providing that outside consultant exposure.
So previously, or prior to starting my own consulting firm, I spent six years in an operating partner role at a Chicago-based venture capital firm, and we focused on healthcare and really digital advertising technologies. And so, the work that I was doing with them was within the healthcare space startup’s entrepreneurial environment.
Amanda Schleede 3:22
Prior to that, I had a number of years at large consulting houses really focused on the healthcare industry. So for me, as I’m aging myself by saying this, the last 25 years of my experience have been on business operations within the healthcare space. So focusing on biotech pharma and the payer-provider space. And so, really, when COVID itself hit, I went and connected up with Becky. I pivoted my business, which was Consult27.
Amanda Schleede 3:48
We created Vital Circle, which is web-based, so it’s a downloadable app, but it’s a web-based app focused on daily symptom tracking of COVID-19. And then, in addition to that, we have added in contact tracing technology, and I know that’s a buzzword for right now, but also usually a high-stress point for employers, but we have developed and implemented a contact tracing device that does not use GPS it is no way uses any biometric data, so you’re not getting like a Fitbit where you’re getting steps and heart rate and all that stuff.
We have no dependency on cell phones. Yeah, and our and our really our overall goal is to provide organizations with data and analytics to really reduce the potential for employer exposure and, within the manufacturing, standpoint was what we’re gonna talk about today is really, reducing the potential for factory or manufacturing shutdowns or department shutdowns.
Sam Gupta 4:47
Okay, love it. Obviously, that’s a big theme right now. So you are definitely helping in a big way. But we are going to be digging deeper into all of what you mentioned because that’s a pain point right now before we do that one standard. A question that we have for all of our guests is going to be your perspective on business growth. So what does growth mean to you, Amanda?
Amanda Schleede 5:07
Obviously, there’s the financial side of it, if you’re looking at from the financial aspect of CEO, CFO, it’s like, how do we, in this pandemic state, continue to grow, the services and the offerings that we have, and really continue to build our business, but I also see growth from an organizational standpoint as to how do you consider or how do you increase the loyalty of your employees to you? There’s a ton of studies out there about, from a human resources standpoint, about how to lose an employee and the cost of bringing that new employee on and getting them trained, and really what the cost is when people leave.
So for me, it’s not only the growth of, okay, we need to get ten more clients. So we need to hit a revenue number of $10 million, or whatever the actual physical numbers are there, but also looking at like, how do we grow our organization internally? And how do we provide an environment where our employees have a loyalty to the brand into the name and long-term employment? And then also how do we grow and get them to understand that we as an organization are really focused on them individually and their health and welfare and wellness?
Sam Gupta 6:14
Okay, amazing. So we are going to go back to the manufacturing aspects and contact tracing as well. So yeah, only if I’m the manufacturing CFO, and I have no idea what contact tracing is and why I should care. Tell me what that is.
Amanda Schleede 6:27
Okay. So contact tracing is a fairly new thing in the US. There are really, as I see it, three ways in which you can do contact tracing. So number one is the person-to-person contact tracing. So you physically have a person who picks up the phone or is doing an interview of another individual. The other way we can do it is through cell phones. So through GPS pinging or phones to phones, the downfall of that is, you can turn your Bluetooth off on your cell phone, and it’s not being traced.
And then we have device contact tracing, which is what we focus on but is really, it’s just a device to device looking for another device and recording, what is the interaction between those two devices, and really all is creating is that data and analytics, i.e., Amanda and Sam were together on February 2, for 30 minutes at four feet, like that’s the data that we need. And overall, the contact tracing side of COVID or any type of pandemic research or data analytics is really the whole idea about if we have a situation where we have an employee or somebody in our population, that is symptomatic for in this case, COVID was symptomatic for COVID, or becomes confirmed positive for COVID.
Amanda Schleede 7:40
How do we, with data and analytics, and in real data and information, identify those people that this person has come in contact with, so that instead of one person affecting 100 people, maybe one person has had a significant amount of contact with, say, five people, and then that way, an organization can say, okay, instead of shutting down an entire plant or an entire line, in a manufacturing situation, we only have to identify four or five, six people who we need to say, hey, we need to put you on COVID pay, or we need to have you work from home.
And so, really, what it’s doing is creating a situation where there aren’t these downstream effects of one person who may or may not know, they’re symptomatic or COVID positive at the time, affecting a business. Because we’ve all seen it, the pork industry was hit very hard early on with COVID.
Amanda Schleede 8:29
And we saw how the cost of a pound of bacon spiked to almost $10 a pound. All those things are things that when you’re in a manufacturing situation, and from a financial like CFO standpoint, it’s, what type of investment can we make in a technology that’s usable and usable beyond COVID, but usable, and will provide me with the data and the analytics and the information.
I need to mitigate the risk within my population, so that I’m not in a situation where, I have one person who, is COVID, positive or COVID, symptomatic, and then I need to turn around and say, oh, my gosh, we got to shut down the entire plant and the entire line for two or three days, and we’ve got to clean the plant. And that’s gonna cause us to lose revenue of X number of dollars, instead, let’s just identify that handful of people that we need to put on COVID leave or COVID break, and we can continue business as usual.
Sam Gupta 9:25
Okay, amazing, so let’s talk about some of the verticals. And I don’t know if this is going to be useful everywhere. Do you believe that every manufacturing vertical can take advantage of this technology? Or is this primarily prevalent in the food and beverage manufacturing space, which you mentioned in your description? So walk us through different verticals, and where do you see the usage of this device?
Amanda Schleede 9:48
Yeah, I personally feel number one, I don’t have this grandiose idea that every manufacturing company is going to use our technology, so I’ll put that out there.
But we’ve really felt that we are industry agnostic, we are working with Primary medical groups, we’re working with schools, manufacturing we’ve been doing in-person events during the pandemic.
So really, the ease of our technology itself is so easy to customize, and so easy to roll out that we can really use it in any situation, when it comes to manufacturing, specifically, it really can be used across any type of manufacturing, industry or setting because our devices and because we’re using physical devices, people where there’s no need to rely on your employees, personal cell phones, or even quite honestly, you may have people who don’t have cell phones, or don’t have smartphones that work on your plants. And we want to have a device that is noncumbersome, meaning that, it’s not huge, you can’t get stuck on equipment, that kind of thing.
Amanda Schleede 10:44
What we find is by having a device is basically it’s not basically all it is reporting device to devise interactions is, our devices are small, they’re non-cumbersome, people don’t even realize they’re wearing them. We don’t have to rely on cell phones. And as we know, in many manufacturing situations, you’ve got people who are on the on assembly lines, who are driving large pieces of equipment, you don’t want them distracted with their cell phone with their pocket, a lot of manufacturing situations, I say like, here’s your locker, put your phone in it, put your car keys in it all your loose, apparel, that kind of thing.
We want to make a situation, and we want to create a situation where, number one, police feel safe and that their employers are focused on their health and safety. Number two is that they don’t feel like their privacy is being somehow dug into or known. Yeah, compromise. We have what we call the three Ps. So it’s privacy, protection, and peace of mind. So we’re providing peace of mind to employers and employees that we’re doing something to mitigate the risk of COVID. We’re providing that privacy aspect. And then we’re really just creating a situation where leaders of organizations have the data and analytics they need to make business decisions.
Sam Gupta 12:00
Okay, so I have some background in the medical device space, right. So I’m going to ask you a couple of questions related to the form factor. So how does the device look? Let’s say if I am the manufacturing CFO, and I’m asking my employees to wear the device, what is the form factor light?
Amanda Schleede 12:15
It’s really small. It’s about the size of an apple watch face or smartwatch face. So if you want to think of it that way, and the way that we have actually developed the form factor is, it’s wearable as a bracelet. You can clip it onto your current badge or name badge that you already have for your employer. And that really makes it easy that it clips onto that. We have a strap that goes around a hardhat. So if you’ve got employees who wear hard hats, they can do that, then easily on a lanyard clip onto the zipper of your jacket or uniform.
For schools, we tell parents to just tie into their kid’s shoelaces. So it’s really not a huge device that you’re wearing, like a clip to you on your wrist and that kind of stuff. And the big thing that we are doing is we’re doing real-time contact tracing. So it’s not like you have a device where you’re wearing it for the day. And at the end of the day, you put it in a holder, and then the data gets downloaded, and then you have access to it. We have real-time data, that if you have somebody who does pop up symptomatic or COVID positive, you’re running data and getting the information in real-time.
Sam Gupta 13:20
Interesting. So tell me a little bit about the technology architecture. What is technology? And I don’t know if you are comfortable revealing that? Are you guys using the near-field technology as part of your contract racing? So tell me how the technology works?
Amanda Schleede 13:33
Yeah, so we are using Bluetooth technology, really what’s happening is the device to device, so the actual what we call mini, so the devices that individuals are wearing are they don’t know where they are in the world, they just know they’ve been assigned to a person. And what is happening is as you’re wearing this device, it’s looking for other people or other devices. So it’s looking for the other devices other people are wearing, you know it’s not recording, are you in the lunchroom? Or are you on the plant floor? Are you at the McDonald’s down the street, it’s literally just saying okay device, and they have 12 digit numbers, but it’s easier to talk in smaller numbers?
But device A and device B were together on February 2 for 11 minutes at four feet, that’s what it’s recording, it’s the recording of the devices, device numbers, the date of the interaction, the length of the interaction, and the approximate distance and we can get it down to a shorter amount of distance.
Typically, especially with COVID, people want to look at that six feet or less. So that’s what we look at. And so what’s happening is those devices that you’re wearing, the individuals are wearing are recording those interactions. And then what we do is we actually set up what we call a hub. It’s a cellular hub in the plant facility, and we plug those in there a plug and play. So literally, I say plug and play, we literally go in, we plug them in the wall, and we add it here to the wall, and we’re done.
Amanda Schleede 14:50
We don’t have to log into a Wi-Fi system or anything on the plant floor or manufacturing floor and what happens is whenever a device that people are wearing and many that people are wearing comes within 150 feet of our hub, all of that data is downloaded off of the wearable device into the hub and then sent to our secure servers. And we have a military-grade server. As I jokingly say, no 13 year old from Russia is gonna be able to hack into it. But again, our devices are all they’re assigned to is a 12 digit device number is assigned to x manufacturing company. Yeah. And then that company knows who they’ve assigned that device to. So it’s really super secure.
So it really does, again, encourage that whole privacy side of the work that we’re doing. And being able to say to an employee, like, we’re not recording where you’re having dinner, we’re not recording where you’re going after hours, I don’t know, if you spent X number of minutes in the break room or all that stuff. It’s literally just recording those device-to-device connections.
Sam Gupta 15:50
Okay, amazing. So obviously, when we look at the Bluetooth technology, Bluetooth technology, from my experience, and again, I’m talking more from the layman perspective. Bluetooth has its issues. Let’s say if I am using the Bluetooth on my phone, and if there are going to be nearby devices that might be in the range, then obviously, there is going to be a little bit of conflict.
And because of that, my device is not going to be able to track the other device, and it might be detecting the device that I don’t want it to detect. So how are you managing this risk? That sometimes, the contact tracing may be there, or the contact may be there. So contact may have happened, but because of the interference with the other device, your hub may not be able to track? Do you guys face this issue? Do you guys not face this issue?
Amanda Schleede 16:35
We have never had that issue. So knock on wood that we don’t, yeah, um, I think the thing what we have done in the development of the physical device that you wear, and then the connection to the hub is that they are all on that same signal. So really, what’s happening in the devices? Wearable devices are only looking for other wearable devices that are getting off that signal.
And then it’s when you come in contact with the hub where the hub is looking for that same signal and pulling all that data off of your device and really clearing your wearable device to add to be able to collect more data. And so we don’t have the issue where we’re connecting with cell phones at all. We’re not connecting with your Bluetooth speaker or with your Bluetooth earphones or anything like that on your cell phone.
This is a different level of Bluetooth. And as you say, your the layman’s Bluetooth information from your perspective. And this is where I would say, Paul, my developer, I’d say, Paul, I need you to provide the technological side of this, but we have not had any type of situation where we’ve interfered with cell phones with any other type of Bluetooth speakers or systems in workplaces are manufacturing places, we are completely separate from, in a sense that cellular network that would be connected with cell phones.
Sam Gupta 17:50
Interesting. So I wasn’t aware that you had the encoding available in case of the Bluetooth case typically. That’s a problem that I see as a layman. It so seems like you have figured out you know how to encode the specific signal for your hub. And that’s how you’re able to readjust the other devices and not the other Bluetooth equipment that might be in the facility. Because these days, I don’t know if any of the floor equipment is going to use Bluetooth technology as well. Because there could be some interference there as well with those machines.
Amanda Schleede 18:20
Yeah, no, we haven’t had any situations, and any of the manufacturing companies that we’ve worked with today, or even employers who are using any kind of Bluetooth technology, I think it’s because it’s just again, this is where it gets the technical terms. And I raised my hand and said help. But it’s different. I don’t think the right word is wavelength. But it’s a different technology from Bluetooth. It’s not the Bluetooth that we’re thinking of, like, Oh, I want to connect to the Bluetooth speaker in my living room and play music off my cell phone.
It’s really, I believe what the technical term is IoT, but the connection between the same or similar devices like devices. And so, really, our wearable devices are what we are looking for each other. And then what our hubs do is, those are what’s attached like in major, major areas where people like a major, entrance or exit in the manufacturing plant, or even the lunchroom or by the restrooms anywhere where people are going to walk by on a pretty consistent basis. They basically create like a bubble 150-foot to 200-foot bubble around where they’re installed. And really, whenever you walk into that kind of imaginary bubble, the system knows to connect and then download all that data.
Sam Gupta 19:31
Okay, amazing. So one of the comments that you made related to using this device after the COVID, and personally, I just want to be done with COVID. I want to be done this summer, and we are not going to have any more COVID as soon as everybody’s vaccinated. Okay, but you are telling me that the contact tracing is going to be there after the COVID, so tell me why contact tracing me is going to be there after COVID.
Amanda Schleede 19:59
Yeah, I mean no, I think contact tracing is here to stay. I know half of America is probably not going to be happy with me saying that, but I think it’s just a fact of life in today’s environment. COVID is really, I don’t wanna say it’s the first, but it’s the first major pandemic that has hit the United States. I think we’re all learning from that right now. There are future pandemics coming down the pipeline, and how we handle them is really what we’re going to be focusing on.
I think we don’t really think of the flu as a pandemic, but our contact tracing and our symptom tracking, or even providing some type of service like that, whether it’s Vital Circle or anybody else, but providing something to the population of your employees or people, showing that you care about their health and safety. we could have been for years tracking the flu, seasonal allergies, like all of these things, sound kind of dumb now.
Amanda Schleede 20:54
But what do you think about it? These are all things that, over time, we could have been tracking. And, from a financial standpoint, an organization can look at that data and say, Wow, like, we seem to have an influx of flu in December in January, which seems to create a situation where 10% of our staff or are not showing up for work, are there further shifts? What can we do as an organization to decrease that number?
Or what do we need to do as an organization to prepare for the fact that we may need to bring on additional part-time staff or temporary staff to cover those voids? And I think just in general. There are going to be more pandemics. There are going to be more things that we’re going to need to start tracking and tracing. And how do we do that without interfering with people’s personal data and personal information or privacy?
And, the other thing we’ve looked at really is pivoting Vital Circle in the future, because our plan is to not stay in COVID only is, what are those other things that within organizations that we can be looking at? Like what, like the workflow? How are people interacting with each other in the workspace? Or, within the plants, how do we reduce the amount of movement within the space. So there are different things that we can really look out from a data perspective that we see as really the next step with regard to the technology that we have.
Sam Gupta 22:13
So as part of the next question, I’m really going to be interested in that in terms of everything. So I know that you are probably worried about privacy and other things. But as a manufacturing CFO, let’s say if I’m trying to create a workflow where I really want to understand how people are interacting on my shop floor, and I’m trying to capture specific data points, other than just the contact tracing, what all are you able to capture, let’s say, if you were not worried about the privacy,
Amanda Schleede 22:38
If we weren’t worried about the privacy standpoint, we have the capability in the future to turn on the GPS tracking, within, a manufacturing plant or within, the flow and really watch as people interact between what are hubs. So, basically, as people interact and move from one spot to another, and really put up additional sensors so that we can see what their workflow is, what their pattern is. So, do you have the best workflow and pattern?
All of the stuff that we have started working on and really looking at is version 2.0 and a sense of Vital Circle? But how do we look at the flow of an organization? Are we using the right flow to increase revenues and decrease costs? What are the situations? Or where are the people that we’ve identified that maybe there’s a higher risk for them in what they’re doing for from an organizational standpoint? So, we’d have to dig into this a little bit more, but could we use it to be tracking workman’s comp-type claims?
So I think the possibilities are endless, a lot of what I say to organizations, especially manufacturing, but organizations at all is a complete group is come to us with ideas like let’s number one, let’s start mitigating the risk of COVID. Within your organization, like that’s front and center now, like, it’s all everybody’s, talking about it looking at it. So like, let’s do that is step one. And then step two, like, let’s explore together ways that this would be the most beneficial for you as an organization. And we’ll work on we’ll develop that.
Sam Gupta 24:13
Okay, so I forgot your comment, whether this is going to be covered by insurance. Do you know if they might be covering this either today or in the future?
Amanda Schleede 24:21
As far as I know, they don’t cover this, but I don’t think they’re going to in the future. My thing is our service is risk mitigation. And really, any of these services that are out there, this is really a way for an organization to provide risk mitigation to their population. On top of that, in many states, if somebody can prove that they contracted COVID from their workplace, it is actually considered a workman’s comp claim. And so there are situations where and we’ve seen them in the news where, employees are suing their employers because they got COVID on it, and their employer site and so on.
This really the services we provide. And really the idea behind risk mitigation is, how can we provide employers and leaders with the data and analytics, they need to manage their population of individuals on a day to day basis, but then also provide the data and analytics they need, in case they get sued by, an employee for future COVID infection. Or if a workman’s comp claim comes in, they can use this data and information to say here, it’s not like we just throw our hands up and said, good luck, we’re going to figure out, as case by case, like, we actually implemented something, we ask for everybody, we’re all in this together.
Amanda Schleede 25:30
So for everybody to complete these daily symptom tracking or symptom reporting, to let us know how they’re feeling based on that, then, we could do contact tracing and identify who, what individuals and who are the individuals are at most risk that we need to identify and quarantine and separate from the larger group of our population. And so I think it’s an overall financial aspect. Yes, it is money that a company has to spend. But I think the downstream effects of showing your employees that you care about their health and safety, that you’re putting risk mitigation in place. So from your insurance carriers to your workman’s comp carriers, to your lawyers, all of this, you’re really showing that you’re doing something to mitigate the risk of somebody coming in whether they know it or not, being COVID positive, and, infecting your entire employee pool.
Sam Gupta 26:33
Yeah, as a CFO, I’m definitely going to be worried about getting these lawsuits from the workers’ comp perspective. So from your experience, let’s say if I have never had this as a manufacturer, I’m a small manufacturer, and I’m inviting my employee to work on my shop floor, and there may be a chance that they contracted COVID. And sometimes, when these employees are going to claim, if I don’t have data to prove that they contracted because of my facility, then obviously I’m in trouble. So what is the financial damage you are talking about? Do you have a sense of that, by any chance? How much are these claims going to cost? Typically, for a CFO so that I can plan as a manufacturing CFO?
Amanda Schleede 27:17
It’s really a case-by-case situation. I think there are situations where we’ve seen a lot of stuff in the news, where there have been workman’s comp claims, or there’s been an employee, or even an employee’s family who’s come back and sued the organization because their loved one has passed away or died from COVID, or can’t, so, these are all things that I think from a risk mitigation standpoint, employers need to look at, I think, I wish I could put $1 amount on it, I think it depends on, I hate to say this, but who’s the judge?
And what state you’re at, and what are their political feelings? And all of that comes into account, and what are they? It’s on a state-by-state basis. So sometimes there are caps on what people can be awarded and all that. So, I think that is. We are providing and, services, similar charges for us, we are providing a service that is showing people outside of your organization that you are doing something to mitigate this risk. And so, yes, there is a cost to the organization.
Amanda Schleede 28:24
But if you weigh that against, what could be possible or is a forthcoming lawsuit, to be able to, go to, say, a judge or an arbitrator and say, hey, here’s what we’ve done to mitigate the risk. Like, here are the steps we took in place, here’s the application, the process, the procedures, like, here’s what employees had to do, here’s what we did as an employer to we’re all in this together, and there is still a chance that somebody is going to contract COVID.
But it’s not like we just said Good luck and show up for your shift, or you’re fired, we actually put an effort towards it, because it’s better to go into, a lawsuit, arbitration, a payout, whatever that is to say, hey, we did something, it’s not like we’re sitting here going, Yeah, we didn’t do anything. Like we just kind of told everybody you got to be here, first shift, and good luck, what we did is we actually looked at what is the best way that we can mitigate that risk.
Amanda Schleede 29:14
And really, we look at if we look at a manufacturing plant, so let’s say, we want to look at their whole health protocol plan. And so it’s not only just what are the daily symptom of how are you feeling today and who have you had contact with, but let’s also look at on-site testing, follow up telemedicine services, when people arrive, what is the arrival process, are people just standing all in one big area out of the cold packed in a room or are people social distancing are people walking in and having a quick like, temperature check, and proof that I’ve done a check-in for the day.
We’d like we have an authentication screen that people can show and then that way, individuals are able to, get into their spaces quickly and safely. So it’s the full mix of like, what is the whole protocol that you as an organization has set up? And how are you implementing that across your population or shifts of people?
Sam Gupta 30:11
Okay. So tell us a little bit about the manufacturers who might not be familiar with the guidelines in terms of what they need to do to prevent COVID in the facility. Do you have any advice on that guideline?
Amanda Schleede 30:22
Yeah, I think I met a lot of it is, making sure that employees themselves are social-distancing and following the rules or the guidelines set by the CDC. I think it’s not only limiting people to be six feet apart in their workstations and all that, but it’s really thinking about, what is the process as people get out of their cars and enter into the plant? How are we setting up break times, and are people taking 200 people off the plant for sticking them into a small room to eat lunch next to each other?
But for the rest of the day, they’re six feet apart. So it’s thinking about that whole process. And then I think it’s also almost overstepping what you think, would be a great idea for in the sense of sanitation side of it. So are we providing enough sanitation stations?
Amanda Schleede 31:07
Have we provided enough touch-free situations were, think about when you go into a bathroom, and you go to wash your hands? like, Is it an automatic soap dispenser? is it is the sink, automatic inserting up, or am I touching everything as I’m going through this process, because if I’ve now sanitized my hands, and I got to touch the faucet and turn it off, and then touch the paper towel holder, like all of that stuff is things you need to think about.
So I think it’s, looking at that whole, as we call the whole health protocol of what’s the processes, people come in? How are we keeping them safe throughout the day? What are their processes going out? And then also in a manufacturing situation? Because many of them were on multiple shifts? What are we doing about cleanliness and cleaning, and sanitizing between shifts? So we’ve had a manufacturing client who had this situation early on, where they had three individuals who were all forklift drivers, but it worked on three different shifts, that became symptomatic. And what they realized is that in-between shifts, they weren’t doing a good enough job or even thinking about sanitizing inside the forklifts. So the guy on the first shift was symptomatic and COVID positive.
Amanda Schleede 32:18
And unbeknownst to him, he had no contact and a sense of the second and the third shift, but because we were able to track how it was the first shift, forklift driver and the second shift work, and the third shift forklift driver that became COVID, symptomatic and positive. They realize that in between shifts, they weren’t wiping down the inside of the forklift, they weren’t all the candles, and all that stuff they used to wipe down wasn’t being done.
And so the next shift was coming in and just grabbing it and go, and it’s just, here’s the thing we all have to remember, it’s human nature, like, we have had years of muscle memory training about just shaking hands, hugging people standing close in line. And so it’s all about like, really kind of looking back at what are the things that we in, I don’t wanna say, say, take for granted. But the things that we’ve just normally done, that we now have to be more cautious and more apparent about how that interaction is happening in the world.
Sam Gupta 33:12
Amazing. So that’s it for today. Do you have any last-minute closing thoughts?
Amanda Schleede 33:18
Yeah, I think my biggest takeaway for everybody here is to do something. It’s better to say that you have done something to mitigate the risk for your population, whether that is using a system like Vital Circle or doing something that really creates a situation where your employees feel there’s health and safety there. But don’t just throw your hands up there and say, this is somebody else’s problem, or it’ll go away in six months, and we’ll be fine.
I think it’s really apparent that leaders, CFOs CEOs need to be focused on how this is affecting my organization and the mental health of my organization. Then I think the other thing to really think about is the HR departments, the Human Resources departments are the ones who are managing this process. And they were busy before. And so now you’re adding even more work and more tracking of people. So like, how can we create a situation where we’re creating the time of effectiveness for these individuals and also helping to lift the load for them?
Sam Gupta 34:13
Okay, amazing. And my personal takeaway from this conversation is going to do not take COVID lightly, and this is the mistake that a lot of us have made. So it is definitely not to be taken lightly. So on that note, I want to thank you for your time, Amanda. This has been an insightful conversation.
Amanda Schleede 34:29
Awesome, wonderful. I’ve had a great time as well. Thanks for inviting me.
Sam Gupta 34:32
I cannot thank our guests enough for coming on the show for sharing their knowledge and journey. I always pick up learnings from our guests, and hopefully, you learn something new today. If you want to learn more about Amanda, head over to Vital Circle. She can help implement a full health protocol plan for your organization focused on COVID risk mitigation, daily symptom tracking, contact tracing testing, and telemedicine services for your employee population. Links and more information will also be available in industrial notes.
If anything in this podcast resonated with you and your business, you might want to check out the related episodes, including the interview with Carol Marzouk from Leadership and Soul, who discusses how to uncover and correct lingering toxicity before it extends your business growth. Also, the interview with Ben Baker, who discusses how internal communication influences growth. Also, don’t forget to subscribe and spread the word among folks with similar backgrounds. If you have any questions or comments about the show, please review and rate us on your favorite podcasting platform or DM me on any social channels. I’ll try my best to do this one personally and make sure you get help. Thank you, and I hope to catch you on the next episode.
Outro 35:45
Thank you for listening to another episode of the WBS podcast. Be sure to subscribe on your favorite podcasting platform, so you never miss an episode. For more information on growth strategies for SMBs using ERP and digital transformation, check out our community at wbs.rocks. We’ll see you next time.