Last Updated on November 27, 2023 by Sam Gupta
In this episode, we have our guest Clay Coleman, who discusses the importance of a quality management (QMS) system. And why it matters for manufacturing and distribution companies. We also had a chance to discuss what manufacturers need to know about starting their ISO and QMS journey. Finally, we discussed how American Petrolium Institute (API) for Oil and Gas differs from other industries’ ISO needs.
Chapter Markers
- [0:00] Intro
- [2:09] Personal journey and current focus
- [5:54] Perspective on growth
- [7:03] Why quality management and QMS matters
- [12:19] What small businesses need to do to prepare for ISO
- [21:06] Pre-requisites before starting the ISO journey
- [24:25] ISO 9001 vs. American Petroleum Institute (API) Spec
- [27:20] How oil and gas quality standards differ from generalized manufacturing
- [36:58] Closing thoughts
- [38:04] Outro
Key Takeaways
- A quality management system forces a company to sit down and identify all of the little tactical steps involved in creating each of the processes pertinent to your company’s order fulfillment lifecycle.
- Even if you’re a small shop with three leaders and three workers, you still need to start with that org chart. You need to identify who’s responsible for what aspects of the company. And then add to your designees responsibilities as the Quality Manager and then dive into one of the first sections of in this example API.
- QMS is the quality management system, which is your book, a tier-one quality manual, supported by tier two procedures and work instructions, documented by tier-three forms and records of standard ops. So it is all written procedures that you can then leverage whatever tools you need. You don’t need an ERP system to adhere to a quality management system. You can do it all with Excel and by hand in a binder.
- At the end of the day, the quality management system is not simply undertaken. A quality management system needs to be thoroughly vetted by the decision-makers in your business. And if it’s seen that value is there, there’s a number of different ways to do it. A small businesses can become ISO or API certified without having to invest the fortunes. We’ve seen, with a few companies able to operate in industries with barriers of entry, such as quality management certifications.
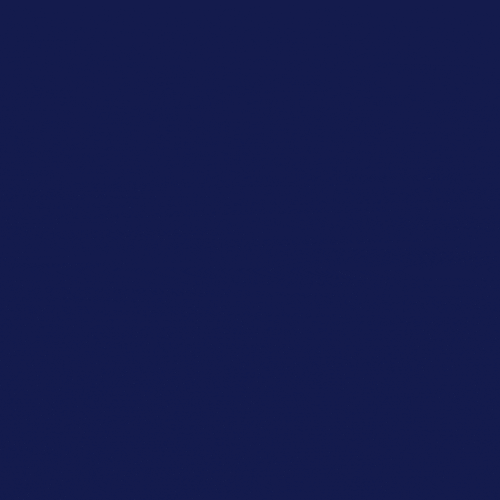
Subscribe and Review
Apple | Spotify | Stitcher | Google Podcasts | Deezer | Player FM | Castbox
About Clay
Clay Coleman is an expert in international business development, process, and strategy specialist. He has 10 years of experience in IT / Quality Management System implementations, analyses, and advisory services.
Resources
Full Transcript
Clay Coleman 0:00
It was very, very daunting. Seeing binders of here’s how to do a job and learning that there’s not one standard format that you have to adhere to was the opening of the door to unbox our Schlumberger engineers and start getting the innovation company like crazy out of our comfort zone.
Intro 0:26
Growing a business requires a holistic approach that extends beyond sales and marketing. This approach needs alignment among people, processes, and technologies. So if you’re a business owner, operations, or finance leader looking to learn growth strategies from your peers and competitors, you’re tuned into the right podcast. Welcome to the WBS podcast, where scalable growth using business systems is our number one priority. Now, here is your host, Sam Gupta.
Sam Gupta 1:02
Hey everyone, welcome back to another episode of The WBS podcast. I’m Sam Gupta, your host, and principal consultant at a digital transformation consulting firm, ElevatIQ.
Managing the quality of your product is not only required to provide a consistent customer experience. It will also be a requirement by customers and regulatory bodies in specific industries. The necessary amount of effort in getting certified and audited can not be underestimated, with significant financial risks for non-compliance.
In today’s episode, we have a guest Clay Coleman, who discusses the importance of a QMS system and why it matters for manufacturing and distribution companies. We also had a chance to discuss what manufacturers need to know about starting their ISO and QMS journey. Finally, we had an opportunity to discuss how API for oil and gas differs from other industries.
Let me introduce Clay to you.
Clay Coleman is an expert in the international business development process and strategy specialist with ten years of experience in IT and Quality Management System implementations analysis and advisory services.
With that, let’s get to the conversation.
Hey, Clay, welcome to the show.
Clay Coleman 2:07
Hey, Sam, how are you doing today?
Sam Gupta 2:09
Okay, just to kick things off. Do you wanna start with your personal story and what you are focusing on these days?
Clay Coleman 2:16
Yeah, absolutely. So I’m Clay Coleman, and I met Sam through a colleague of mine, Wayne Sadin, who I was working with over at Orion. And my journey to the discussion we’re gonna have today about being a quality management field. I just love it as I come from a background of analyzing it and have the opportunity to take a company from ground zero to an international provider of Donald tools. So just a little bit about my background to dive into that I started out as a pricing analyst for Georgia Pacific for the railroad’s division. And we did not have software for it. It was all macros, Excel, Access databases, and having to use OCR and stuff. So I went into consulting with a subsidiary of Capgemini called Sogeti and moved to Houston to focus on the oil and gas industry.
Clay Coleman 3:19
It was in that focus that I was exposed to Schlumberger and a number of other different large oil field service or oil companies in the area doing different engagements like SharePoint migrations ERP implementations. When we got into advisory services, where a lot of it came into reviewing and simplifying processes from that work, I went to Weatherford to go in the house as a process engineer. And then I was given the opportunity to help launch a company called Frontier Oil Tools.
It was a group supporting a company that was purchased by Schlumberger in 2010 or 2009 employees over in Russia and Eastern Europe with what we viewed in the US as commoditized tools, selling downhole tools that are used in the construction and completion of an oil well had certain barriers of entry. One of which was to become an API, which is the American Petroleum Institute, certified manufacturer of downhole tools and also certified provider of services for the install of said tools. But for today, we’re going to talk about manufacturing in particular.
Clay Coleman 4:48
I spent about six years long, six and a half years with Frontier Oil Tools, before moving on to go to a large public group to work on an ERP implementation with Microsoft Dynamics. And since then, I’ve helped launch a little company called GasLogix, where we are distributing natural gas by-products.
We’ve bought ownership rights to natural gas scrubber and storage group south of here. And we are doing a little logistics and distribution network set up across the US and the entire platform. I’m leveraging for that Zoho One.
So we’ve been asked to introduce an ISO 9001 quality management system for that energy company that we bought distribution rights for. And now I’m diving back in. So that kind of round circle with the Microsoft implementation and then working back on quality has brought us to conversations you. And I have been having back and forth, Sam, and I’m excited to dive into it a little bit today.
Sam Gupta 5:54
Okay, and I’m super excited to dive into that as well. But before we do that, but one standard question that we asked every single guest, and that is going to be your perspective on growth. What does growth mean you, Clay?
Clay Coleman 6:07
Growth, to me, means the ability to fulfill an order. You can go out there and sell, sell, sell. But if you can’t meet your obligations of the sale, whether that’s providing a product on time, a service that gets completed on time, etc. If you’re not able to live up to your obligations, you cannot grow in enabling the ability to meet those obligations as sales ramp-up is the creation of standard operating procedures, resulting in repetition. And those repetitions create data with which we can assess and continuously improve. I firmly believe that a quality management system forces a company to sit down and identify all of the little tactical steps involved in creating each of the processes pertinent to your company’s order fulfillment lifecycle.
Sam Gupta 7:03
So you know, as you mentioned, from the growth perspective, that growth is comprehensive. It’s not just sales, and marketing is slightly bigger than that. And quality management is obviously going to be a big puzzle of that. And you mentioned the quality management forces companies to think about their product quality overall and forces you to improve the process and efficiency as well. But let’s look at some more benefits. From the quality perspective, let’s say if somebody is starting on the quality management journey for the first time, why should they care about QMS?
Clay Coleman 7:34
So quality is kind of a big animal to tackle. And I think we want to start with identifying what a QMS is, and that’s a quality management system. Okay. And so ISO, the international standards organization as a standard called ISO 9001, is the blueprint of a quality management system that you would need at your company. And that blueprint would serve as each of the little processes. Some may have a lot of details. Some may not think that you need to have documented for your company with which you can standardize, implement, etc.
So I’m going to speak to API because that is where my experience stems in working with the American Petroleum Institute. The only difference between their quality management system requirements and ISOs is the addition of some oil-specific topics. So if I was looking to implement an API quality management system, I would go to API. It is the oil and gas industries regulatory body that provides certification to different applicants from API, they have their quality management system, and that provides your outline of processes that you need.
Clay Coleman 9:02
Now, you can take a look at that. So, in particular, this one is API spec, Q1 ninth edition. And that covers the ISO 9001 2015 edition, quality management system requirements that adhere at all industries in the US, well, internationally, API is pertinent to the US. At the end of the day, what you’re going to do is you’re going to get on API’s website. And you’re gonna download that quality management system spec.
When you first look at it, it’s just gonna look like an outline. And you’re gonna see a couple of high-level topics of quality management system requirements, a quality management system, what is your quality policy. And whatever your objectives may be, it’s a lot of high-level stuff in those first five or six sections. As you continue to look, you’ll eventually come to section five in reference to what we’re speaking about API spec Q1 for a quality management system, section five product realization. We’re going to talk a little bit about that when we dive into some specifics within here.
Clay Coleman 10:12
But at the end of the day, and navigating this first view, you’re looking at a tier-one quality manual. And that’s your high-level overview. We have all of these different processes documented. And here’s a little excerpt about what it is in each of those sections. In this example, section five has an association with what are called tier two and tier three documents. Tier two is your procedure or work instruction that accompanies that reference of the topic. Tier three is the form that gets filled out in conjunction with performing that action to record that transaction and serve as a record for you following the process.
So when we look at a quality management system from day one, here’s what I want to implement at the company. I’ve gotten in, and I now have API spec key one’s quality management system requirements. And as I read through each of these different paragraphs or subjects. I see that there are a number of tier two procedures that need to be documented that may or may not have an accompanying form to serve as a record of performing that procedure. We got to connect the dots top-down, bottom-up, at the end of the day, the high level of what that does, taking that view, to assessing the scale of the project. It’s going to be to implement a quality management system for your business allows you to read this 30 something page guide as much more than that, because not to scare anyone.
But a quality management system involves the documentation and standardization of all the processes in companying how your business operates from quote through a collection of invoice receivables,
Sam Gupta 12:19
Okay, so that’s a great description, Clay. So let’s say if I have a manufacturer or distributor. Also, let’s say they are a lifestyle business, and typically, lifestyle businesses are going to be that are less than $25 million in revenue. And they are typically founder-run businesses, right. So that’s how we describe the lifestyle business in the finance community. So let’s say you have a lifestyle business. And they don’t really have any of their processes documented. And they sort of have processes, but they are not as standardized. Everybody has their own way of following the processes. So what do they need to do to prepare to start the journey for ISO?
Clay Coleman 13:01
I think the first thing that in this example is that most companies need to do, who is asking for this. You got to get your decision-makers in a room and have everybody on the same page top-down that you want to implement and adhere to the quality management systems. So that’s step one. You need to get all of your decision-makers in a room, listen to the Ask, ask yourself, why do we need a quality management system? Is it worth it? And if so, you need to define some roles, responsibilities, and expectations of members of your team for the implementation of this system.
So you’ve got to define your actors and who’s going to be responsible for drafting and implementing the quality management system. And a lot of us in this WBS group have done different project management engagements. They are pretty familiar with a RACI chart you need. Even if you’re a small shop with three leaders will say and three workers, you still need to start with that org chart. You need to identify who’s responsible for what aspects of the company and then add to your designees responsibilities as the Quality Manager. Then you need to dive into one of the first sections of in this example API.
Clay Coleman 14:50
QMS details the responsibilities of a quality manager. You have to have your president or leader of the company sign off in support of that designee. And in the implementation of this QMS. So that’s step one, got to get everybody on the same page, got to get agreement top-down. You got to get somebody assigned to the project and granted the authority to do what they need to do to get this implemented appropriately. Or you need to work with the different business units that are going to be responsible for individual paragraphs and references within the quality management system.
Sam Gupta 15:05
Okay, so from your perspective, is QMS some sort of ERP system? Is that a software tool? Are you referring to the documentation and collection of a spreadsheet to call this system? What is your perspective on that?
Clay Coleman 15:27
So QMS is the quality management system. And the quality management system is your book. A tier-one quality manual, supported by tier two procedures and work instructions. It is documented by tier-three forms and records of standard ops. So it is all written procedures that you can then leverage whatever tools you need. You don’t need an MRP system to adhere to a quality management system. You can do it all with Excel, and by hand in a binder. I wouldn’t recommend it because there are retention periods on records, and yada, yada, yada, it’s pretty old school.
But you can still become certified without having to invest in any of these high-dollar tools. So when I talk QMS, I’m talking about your quality management system. It is your tier one, tier two, and tier three sets of documentation. Its purpose is to be wrapped up to serve as your standard operating procedures for each aspect of the business.
Sam Gupta 16:39
Okay, so let’s say if I’m going through tier one, tier two, and tier three. And I can relate that tier one is probably going to be a high-level summary of some of my processes. So what specific standards am I going to expect in each of those sections as I’m going through that document?
Clay Coleman 17:00
So getting into, and I’m going to talk API because there are ISO references throughout. It’s basically ISO with some oil and gas spefic additions. The first set of your tier one manual is to highlight what a quality management system is and its goal. What our company objectives are and what are our company’s high-level KPIs. And who’s responsible for the maintenance and continuous improvement of this quality management system.
After the first handful of paragraphs, you’ll then start getting into detail. As an example with API, Section four is all covering the intro pieces we had just discussed. Once you hit section five, section five is about product realization. Within product realization, you get a number of subsections 5.1 being contract review, so a review of the contract you just sold, whether that’s to provide a product or provision, a service, risk assessment, design and development inputs, purchasing, and then it walks through your manufacturing, how you’re, if say, if you’re making a product, where are you taking your measurements and validating that the product conforms all the way through that process, the way you need to look at it is it starts, everything starts high level, and then it just keeps getting deeper and deeper and deeper into the weeds.
Clay Coleman 18:35
So all of section five is going to be about provisioning that product. Then once you finish with that in continuing the example of API, once you hit section six, it’s all about your quality management, system monitoring, measurement, analysis, and improvement. So it’s about continuously improving this document. So Section four and starts in Section four. But in an API quality management system, Section four is your intro, your high-level overview of company application. Section five is the production and provision of whatever it is you sold.
And then section six is all about how we maintain checks and balances of this quality management system, ensuring that we’re doing what we say we do in our providing record of it. And section six is where you get into doing your own internal audits, hiring whichever certification body in this example API for external audits, etc. Once you’ve gotten through that, that’s the end of the quality management system. It’s an intro. Here’s how we do all this stuff. So as you can imagine, section five is where a lot of information is in section five is the primary target of the audit.
Clay Coleman 19:58
Then, section six is Okay, we’ve implemented this to IMS, how do we ensure that we adhere to it, because, as you said earlier, and I saw this at whether for a lot because whatever was made up of over 100, different acquisitions, people kind of want to work, how they’re comfortable. And the quality management system in forcing your company to document and standardize its procedures, which means all of your workers or those that are affected by those procedures now need to adhere to what’s documented, it can be a pretty radical change.
That’s why I say step one is getting all of your decision-makers in a room and assessing is it worth it for WBS and my concept of growth, meaning you can’t grow unless you’ve got the proper foundation, I would say a quality management system in forcing you to standardize and document all of these procedures and examples we just went through, creates a foundation with which you can then edit or build upon.
Sam Gupta 21:06
So give me some examples of those checks and balances that you mentioned related to different processes that I may have in my business. I get the idea overall, in terms of what you’re doing, but I’m still looking to see whether I have those checks and balances at this point of time, as they relate to my processes and purchasing as they relate to improving success in design, I may not have some of the approvals that some authorities might be looking for. So what are the examples of those checks and balances that I should be expecting, and I should probably have those in place before I embark on the journey of ISO?
Clay Coleman 21:42
Well, you know, I think a really good example that’s got some broad applicability for the context of our group with WBS is to talk about a sales contract review. So this and the order fulfillment lifecycle is when we are converting a quote to an active order. So we’ve quoted a customer, they’ve responded, we’ve gone back and forth with whatever adjustments, negotiations, etc., may be necessary. We’ve sent them the revised final details gotten in writing confirmation, that yes, we are ready to go on this quote, order it, etc., or begin the order.
A sales contract review, in an example, would be as simple as a one-page printout that just says customer name, quote, number details of the order, a little summary of the back and forth for whatever changes were required is, quote, accurately reflected. And this is all an internal sign-off. Put it in a folder or sign off, scan it, and put it in a digital folder. I prefer attaching it to any ERP system.
Clay Coleman 22:54
But I’m not going to speak about ERPs in case that’s not being used. It just needs to be related to the order at hand, the quote converting to order, and now you’re ready to put it into fulfillment. And so in the manufacturing world, I would have taken this formal quote, I would have attached my correspondence from the customer, I would have attached my sales contract review, which has the designated salespersons sign off because he’s accountable for yes, these details are correct to then release to my manufacturing lead to put into motion.
And that would kickstart the checking of inventory for material and buying new material if required. The print up of the work packet, the drawings, the getting it on the machines, yada yada yada everything downstream from there, but the value that a sales contract review brings to the table, as I think a really good example for something that ISO is going to be looking for is it holds that salesperson accountable for what is being pushed through your company to fulfill.
So if that guy sold this specific liner hanger to this company, all of the accompanying details that are in that quote, required for accurate fulfillment, have been checked off and approved by the salesperson, and it transfers the accountability to whoever your designated individual may be in your company. Instead of it being well, a bunch of finger-pointing when something goes wrong. Well, you did this wrong. Well, you signed off on it.
Sam Gupta 24:25
so let’s talk about API. So obviously, I can relate that API is probably going to be slightly more specific than ISO 9001. And there are going to be some oil-specific standards. So let’s say if I was doing the generalized manufacturing, and now I’m trying to move to oil and gas, okay, then I have no idea how oil and gas works. And you are trying to teach me how oil and gas specifications are going to be different from generalized manufacturing. So what are some of the things that I should be expecting in API?
Clay Coleman 25:03
So what’s great, and I would imagine it has similar applicability in medical and aerospace manufacturing. American Petroleum Institute provides what’s called a conformity matrix. And it is a spreadsheet outline of all the different subsections of a requirement referenced within specific paragraph x that need to be documented somewhere. And when you’ve finished creating all of these documents, you populate this conformity matrix with reference pointers to your internal documentation as to where that requirement is met.
That conformity matrix on the very left-hand side shows paragraph 5.1. Point two in the API requirement is 7.2, point one A through D. In the ISO 9001 2015 edition reference, it’s a quick scan if you’ve got familiarity with ISO, and you want to go into an industry-specific standard like API in this example, the conformity matrix by that certifying body is where I would start because as you review that spreadsheet, in the case of API, they’ve highlighted where requirement has no reference to an ISO requirement.
So it’s an outlier. ISO does not require this, or where they’ve identified that API doesn’t care about this requirement, even though it’s an ISO. So not required in the API paragraph. But this is an ISO number. So it’s a cross-check of what’s different. And it shows what additional details would be needed. On top of a standard ISO 9001 quality management system, that API would require to extend their certification. So a company can earn, you know, I just like to roundtable that a company can earn an ISO cert a number of different ways. It’s the industry-specific regulatory bodies that leverage that ISO cert and then add to it for their certifications.
Sam Gupta 27:20
Great. So from the process perspective of API, Are there going to be any differences in terms of how I should be capturing my transactions? How should I be recording my vendors? How should I be documenting my quality standards in the case of oil and gas? Are there going to be any differences from the general manufacturing?
Clay Coleman 27:36
No. So what that was one of the most difficult things for me to learn, especially being that my initial exposure to quality management systems was through Schlumberger, who basically had every step of your role, how to perform your responsibilities, and what those KPIs to measure that performance would be documented. It was very, very daunting. Seeing binders of here’s how to do a job learning that there’s not one standard format that you have to adhere to was the opening of the door.
To unbox our Schlumberger engineers in start getting the innovation pumping like crazy out of our design department, we took a lot of unnecessary step-by-step procedural with accompanying you need to enter in X, Y, Z in ERP, system area, etc. And just simplified it down. So to answer your question, when you’re looking at writing a quality management system, and you approach it with ISO first and are then wanting to specialize further with API certification, you can keep your ISO documents and gap-fill whatever those missing requirements as identified for the conformity matrix we were previously discussing have pointed out that ISO QMS will suffice for an API certification. As long as you’ve added in the additional requirements, that API is documented for the conformity matrix.
Sam Gupta 29:25
Okay, so how does the follow-up process look like so? Let’s say if I’m applying for the ISO, you know, I’m probably going to have some sort of inspector who’s going to review my process. So walk me through the journey, how the process and process of review and submission looks and how our follow-ups going to be year by year, and what, as a business owner, I need to do to make sure I have everything that my auditors are going to expect
Clay Coleman 29:52
in preparation for going down the road of implementing a quality management system. You need to know upfront that year over a year. You’re going to be internally and externally performing checks on yourself. Some industries don’t require an annual formal audit, whereas others do. And in some of those cases, others do until you become tenured at five years, or what have you. In approaching the implementation of a quality management system, you need to really, as a business owner or leader, look at it as we are now going to have written documented standard operating procedures that we need to adhere to if our QMS says we do it, we need to show it.
And if there’s the ability to show a record of having performed certain requirements, there needs to be an accompanying way to record that, that effort with API, the way this whole thing works is okay, your company has determined that yes, it is worth it. There’s value in implementing an API quality management system. We’ve gotten the spec from Q1. I’ve designated someone in our leadership group responsible for this project.
Clay Coleman 31:18
And I’m going to recommend if you’re starting from scratch, doing a little searching and finding one of these API quality management system training groups, kind of similar to prepping for a PMP exam, where it’s a little three-day overview because then that’ll provide you some templates. So you don’t just sit there spinning your wheels, trying to create all this stuff from a blank canvas. That’s not against the rules. If you’re provided something, and there’s not a legal issue there, you can use it. API doesn’t care.
But you need to have the framework for tier one, tier two, and tier three blown-out quality management system. By downloading the spec, you’ve got the guide to write your tier one manual. I’m just going to pause here and reiterate that you’ll save yourself some money, whether that be from time spent effort, etc., by going to one of these overview courses that provide you with templates and material with which to construct this, because it’s also going to get all of your verbiages lined up because an audit, they’re going to want to see your designee go full understanding of what a quality management system is why we’ve implemented it, how are we maintaining it, etc.
Clay Coleman 32:00
So to pick back up, you’ve gotten all your stuff, you’ve now written your tier one, tier twos, tier threes, you’ve practiced it. You need different industries to have different lengths of time before you’re eligible for audit, that it has to be an implementation in oil and gas, it’s six months. So you have to show records of this being implemented and followed for a period of time.
You then go to that governing body and submit your QMS tier one, tier two, tier three, your record of implementation, because you actually have to do a sign-in sheet for meetings to show that you had a meeting had a record of it, and record of conducting business in conformity with your quality management system. So whether that be inspection logs, if you’re a manufacturing company, and all of the job packets, it’s the details that are in that job packet.
Clay Coleman 33:44
All those records need to show that you have been doing what your standard operating procedures are written as for that period of time, API will assign an auditor, an audit date, and there will be some fees. The fees on this it wasn’t ridiculous for American Petroleum Institute. I believe it was under $5,000. It was all in on the certification fees paid to API, including the formal spec that I had to have from them. And so I mean, it’s you know, it’s not cheap. But that’s API.
I’m assuming manufacturing and aerospace are probably in the same area. But that’s, that’s why I say you know, it’s a lot of effort. But it’s not unattainable for a small business. This, you just have to be willing to commit to documenting all the nuances of how you conduct your business, implement it, and create records of following said process.
So rounding it up, you’ve written it, you’ve implemented it, now you’ve submitted to become certified. You’ll then have an internal audit that you conduct yourself, or you can hire a third party to do that. There are different ways, and then you have your formal audit where they review the performance of your internal, which is why I say you can hire someone. There are different strategies there that we can discuss later. And then also all the meat and potatoes of your tier one, tier two use tier threes, and nobody’s going to pass it on the first round, they’re going to present to your findings and findings need to be addressed, because it’s in nonconformity. In other words, you said you were going to do this, and you’re not, or where’s the record, etc.
Clay Coleman 35:30
And you have to do an investigation, identity why, and document what happened? Do we need to change any? And what was the impact? Does there need to be a change? How are we changing? How did you change? And how are you monitoring to ensure that there’s no backsliding? That’s the way that you address these findings. You then go year over year with that certification body where they’re coming in and checking in on you very much in the same style as your certification on it.
But at that point, it’s just maintaining. So once you’ve addressed those findings, and your first certification audit, to the satisfaction of the governing body, I say that because there may be some back and forth. But you’re basically logging into a website and attaching evidence of here’s how we changed this. Here’s how we’re following it. And they go, yes, Frontier Oil tools have sufficiently corrected these nonconformances. They have a sufficient quality management system for the API reference spec Q1 ninth edition for quality management systems. They are now issued a certification of conformance with sets back. Long story short, now you can advertise you’re an API certified manufacturer and provider of tools, and you’ve gotten past that barrier of entry required and upstream oil to get your tools down.
Sam Gupta 36:58
So that’s it for today. Do you have any last-minute closing thoughts?
Clay Coleman 37:01
At the end of the day, the quality management system is not simply undertaken. A quality management system needs to be thoroughly vetted by the decision-makers in your business. And if it’s seen that value is there, there’s a number of different ways to do it. In small businesses can become ISO or API certified without having to invest the fortunes we’ve seen, with a few companies able to operate in industries with barriers of entry, such as quality management certifications.
Sam Gupta 37:45
I just wanted to thank you for your time. And there are some serious insights here that manufacturers and distributors can definitely take advantage of. So thank you again for that.
Clay Coleman 37:57
Absolutely. And thanks for your time today, Sam. Happy to pop in here and share some thoughts on quality management systems.
Sam Gupta 38:04
I cannot thank our guests enough for coming to the show and sharing their knowledge and journey. I always pick up learnings from our guests, and hopefully, you learn something new today. If you want to learn more about Clay, head over to gaslogix.com. Links and more information will also be available in the show notes.
If anything in this podcast resonated with you and your business. You might want to check the related episodes, including the interview with Max Krug, where he discusses what actions businesses need to take if they encounter product quality or business performance issues. Also, the interview with Ian Pratt where he discusses how to distinguish between the need for additional resources and operational bottlenecks that need to be optimized before investing further.
Also, don’t forget to subscribe and spread the word among folks with similar backgrounds. If you have any questions or comments about the show, you can rate us on your favorite podcasting platform. Or DM me on any social channels. I’ll try my best to respond personally and make sure you get out. Thank you, and I hope to catch you on the next episode.
Outro 39:05
Thank you for listening to another episode of The WBS podcast. Be sure to subscribe on your favorite podcasting platform, so you never miss an episode. And for more information on growth strategies for SMBs using ERP and digital transformation, check out our community at wbs.rocks. We’ll see you next time.