Last Updated on November 27, 2023 by Sam Gupta
In this episode, we have our guest Max Krug, who discusses what actions businesses need to take if they encounter product quality or business performance issues. He also describes how statistical process control (SPC) could help in addressing such issues. Finally, he shares several stories in different manufacturing verticals, where he has implemented SPC processes.
Chapter Markers
- [0:00] Intro
- [2:22] Personal journey and current focus
- [2:57] Perspective on growth
- [3:44] How to accomplish double the growth?
- [4:25] Does SPC help double the growth?
- [10:48] How statistical process control differs from any other data gathering
- [15:21] AI predictive analytics versus SPC
- [21:44] Does SPC need an ERP system, or can it work standalone?
- [24:07] Which industries are the right fit for SPC?
- [28:34] Does SPC slow down the processes?
- [35:23] Closing thoughts
- [36:10] Outro
Key Takeaways
- If we’re getting the wrong measurements, we’re going to get the wrong behaviors, the wrong behaviors, the wrong outcome. So we want to make sure that the processes, we really understand what the next step in the process needs.
- If things start to go outside of normal ranges, and we don’t wait till we have a major problem before we react. SPC helps us understand when a process starts to drift, and we take action before it becomes a problem.
- Statistical process control is about understanding statistically how the process is performing. And if we start to see the process drift, there are rules around what an out-of-control situation looks like or what we call special cause variation, when we have specified variation, we react and correct it before we have a problem.
- Most manufacturers don’t understand with SPC you start with measuring the product, but that’s not the end game. That’s where you start to understand where is the variation in my process, and I want to make sure that the outputs are good every time we produce the product, but the power of SPC is driving it back to the process.
- There’s a measurement called CPK. That measures process capability. And depending on what that data is telling us, it tells us the frequency and how often we should take the measurements. Yes, we want to make sure that long term, the process stays capable.
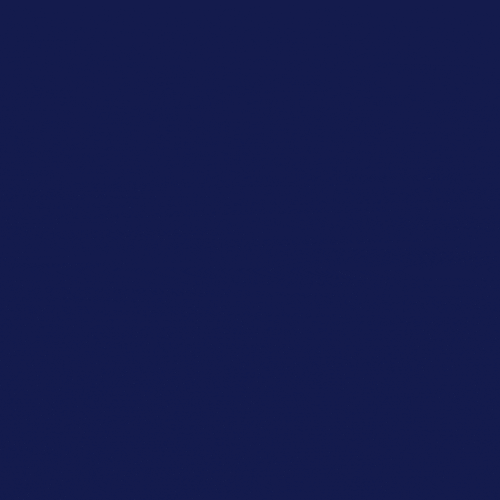
Subscribe and Review
Apple | Spotify | Stitcher | Google Podcasts | Deezer | Player FM | Castbox
About Max
Max Krug, the owner of Future State Engineering, has 35 years of experience in operations, with a focus on manufacturing and distribution companies. He coaches companies to help develop operational excellence strategies and provides hands-on mentoring and implementation support for the necessary and sufficient actions to become a high-performing organization. His education is in Industrial Engineering, and he utilizes Theory of Constraints, Lean, and Total Quality Management techniques to achieve breakthrough performance improvement for organizations.
Resources
- Connect with Max
- Connect with Future State Engineering
Full Transcript
Max Krug 0:00
Leave the process alone if it’s operated correctly and understand when it should take operator intervention to make adjustments and quality will improve significantly just doing those two.
Intro 0:12
Growing a business requires a holistic approach that extends beyond sales and marketing. This approach needs alignment among people, processes, and technologies. So if you’re a business owner, operations, or finance leader looking to learn growth strategies from your peers and competitors, you’re tuned into the right podcast. Welcome to the WBS podcast, where scalable growth using business systems is our number one priority. Now, here is your host, Sam Gupta.
Sam Gupta 0:48
Hey everyone. Welcome back to another episode of The WBS podcast. I’m Sam Gupta, your host, and principal consultant at the digital transformation consulting firm, ElevatIQ.
Growth could be challenging with product quality and process waste issues. You can also see inflated costs and reduced profit margins if you don’t track scrap and waste appropriately. The problem could even be more significant if your measuring equipment is not appropriately calibrated or provide the necessary precision needed by your processes.
In today’s episode, we have a guest Max Krug, who discusses what actions businesses need to take if they encounter product quality or business performance issues. He also describes how a statistical process control or SPC could help in addressing such issues. Finally, he shared several stories in different manufacturing verticals, where he has implemented SPC processes.
Let me introduce Max to you.
Max Krug, the owner of future state engineering, has 34 years of experience in operations with a focus on manufacturing and distribution companies. He coaches companies to help develop operational excellence strategies and provide hands-on mentoring and implementation support for the necessary and sufficient actions to become a high-performing organization. His education is in industrial engineering, and he utilizes Theory of Constraints, Lean, and total quality management techniques to achieve breakthrough performance improvement for organizations.
With that, let’s get to the conversation.
Hey, welcome to the show, Max.
Max Krug 2:21
Hey, Sam. It’s great to be here.
Sam Gupta 2:22
Okay, amazing. So to kick things off, you want to start with your personal story and what you’re focusing on these days.
Max Krug 2:27
Yeah. So what I do is that I help organizations improve their performance. So my focus is really manufacturing companies. I’ve spent my whole career in manufacturing. I do a little bit in distribution, where I’m really looking to help manufacturers improve their business outcomes. And really, I am a hands-on guy working with the leadership, working in the organization to help them understand how we can do things better, how we can get better outcomes, and how we can drive better performance within the organization.
Sam Gupta 2:57
Okay, so tell me, what is your perspective on growth? And that is the question that we ask every single guest that comes to the show.
Max Krug 3:05
So my perspective is, I want to focus on operations to create the capability to deliver what the market needs or what the customers need. Too many times, I see companies go out, get a whole bunch of sales, and they can’t deliver on that, and they just make the customers mad.
So my focus is really, let’s make the internal operations capable of delivering what the customers need, and maintaining stability, and be able to deliver that even through the growth of the organization. So if we have customers that are satisfied now, what happens if we could double the growth of our current sales and deliver what we’re delivering now to our current customers? To me, that’s my focus.
Sam Gupta 3:44
Okay, so if I’m the manufacturing executive, obviously, you are exciting me. Who doesn’t want to double the growth? So tell me how you are going to help me accomplish.
Max Krug 3:51
First, we need to understand from your customers’ perspective, what their needs are, and then to be able to deliver on those needs better than anybody else in the market. So I’m trying to create a decisive competitive advantage by creating the internal capabilities to deliver on those needs, to the extent that no other competitor can, so I want to differentiate or the organization from what the competitors can deliver. Of course, that focuses on where in the operations do we need to have controls to make sure that we can deliver every time to the customers,
Sam Gupta 4:25
Okay, and my understanding of your work as you do a lot of work in the quality and SPC space as well. So say, SPC or quality, how to accomplish double the growth? Or is it the overarching work that you do that helps them accomplish this kind of growth?
Max Krug 4:40
I’m looking at the concepts of process control to help fuel the growth because we want the process to be stable. So what that means is the outcomes are predictable. I don’t care if it’s a manufacturing process, a machining process, a plating process, a sales process, a scheduling process. We want to make sure that those processes are capable of delivering what the next step in the process needs.
So I look at the customer-supplier relationship within the organization and say, Okay, this process. Who’s your customer? Let’s make sure that we deliver everything that’s necessary and sufficient for the next step in the process to complete their work. So I use best process controls an overarching philosophy to say, Okay, what is it the next person needs? Let’s make sure we deliver on that. And that makes sure that the process is capable of delivering on that.
Sam Gupta 5:30
Okay, so I like what I hear, but I need to know more about how this is going to happen. So obviously, you know, I would like my businesses to be predictable. I would like all of my processes to have some sort of KPIs. I have been trying this for the last ten years, but somehow I’m not able to get to the point where I feel comfortable with my processes. So what could be my problems?
Max Krug 6:00
So part of it is what I see in a lot of companies is everyone does understand who their customers are in the organization. Let’s first do is make sure we understand in the organization, who are your customers and really understand what do they need to do their job, then we go back and look at the process and say, okay, is the process able to deliver and I’m a big Pareto principle guy. So what that means is the 80-20 rule.
I would say most companies, I would go and look at 20% of their problems come from 80% of the causes. So if I can focus on 20% of the problems, I can eliminate 80% of the chaos that’s happening in the organization. 20% of your processes are creating 80% of the disruptions in the organization. So it’s all about focus. So if we can go in and look at those process options and put some controls in place, yes, you know, measurements need to be there.
Max Krug 6:56
But we got to make sure we have the right measurements. If we’re getting the wrong measurements, we’re going to get the wrong behaviors, the wrong behaviors, the wrong outcome. So we want to make sure that the processes, we really understand what the next step in the process needs. And so many times, I see people doing things, and nobody’s looking at it. I see it in reports all the time. And companies, oh, we’re generating all these reports. And, okay, who’s looking at the reports? I don’t know.
I just send it out. I’ve been sending out 20 years to this group of 50 people. And I said, Okay, stop doing that. Okay, and then see how many people come back and say, Hey, where’s that report usually send out every week? I didn’t get it this week. It’d be surprised how many people don’t come back and ask for that information. So typically, companies are sitting in what I call a sea of data, we have all this data that we’re gathering about our processes and our systems and our organization, but there’s no data I can see.
So it’s about having data that you can see to make decisions that are going to affect the outcome. And that’s the whole process control concept, right? We just want to have data that’s relevant to make decision-making the most of the other data is irrelevant. So there are very few points in the process, we need to actually understand are working well to make sure that the system or the organization is delivering what they need.
Sam Gupta 8:20
Right. So I completely agree with you there. I was an executive, if I had access to the data that I need to care for, obviously, that’s the ideal place to be, but it’s not as easy to accomplish. In my experience, you know, we have been doing a lot of reports in my organization, if in the ideal scenario, what I would like to do is I would like to have a dashboard where I can see all of my processes, I could see all of their outputs, I could see all of the bottlenecks between the processes, but is there something you have been able to accomplish and some of the engagements that you have done?
Max Krug 8:57
Yes. So we start out by understanding what the vital signs of the organization are. Like, think about your health, I only have a few vital signs I need to look at to make sure I’m healthy. My heart rates are good, my blood pressure’s good, my temperature is good, my breathing rates are good, as long as those are within normal ranges, I’m pretty healthy.
It’s the same in an organization. What are the drivers of your organization? Let’s put some metrics around those. Let’s monitor those metrics statistically and understand. Okay, as long as I stay within normal ranges pretty healthy. If things start to go outside of normal ranges, and we don’t wait till we have a major problem before we react. SPC helps us understand when a process starts to drift, and we take action before it becomes a problem.
Max Krug 9:49
So statistical process control is about understanding statistically how the process is performing. And if we start to see the process drift, there are rules around what an out-of-control situation looks like or what we call special cause variation, when we have specified variation, we react and correct it before we have a problem.
It’s a proactive approach, not a reactive approach. We can look at different processes and really focus on the bottleneck. So, where are the bottlenecks in the organization? We got really tight process controls around those because the bottlenecks dictate the outcomes of our organization. So if we can put process controls in the area where we have bottlenecks, we want to make sure that those processes stay operating within normal limits. Anytime the process starts to drift, we want to make sure we take corrective action to get it back in control before it goes out of control and becomes a major problem.
Sam Gupta 10:48
Okay, so you mentioned the term SPC. So I need to know a little bit more about that. And obviously, as an executive, I’m the CFO or CEO of my organization. Somehow I have figured out how to build the financial statements and how to sell my products, right? That’s the state. I mean, I’m not very good at maths.
So now, you are putting a lot of different terms there. You know, and I need to know more about why that matters, why the statistical process control differs from any other data gathering that I have been doing. For me, it’s just the dashboard. Right? So tell me how the statistical process control differs from just a regular data gathering.
Max Krug 11:32
Okay, so we can look at data in two ways. It’s either forward-looking or backward-looking. Most of the metrics I see in companies are backward-looking. So how did we perform the last quarter, the last month, the last year, and it’s all looking backward, statistical process control is looking forward. So we’re looking forward and saying,
Okay, this is how the process of performing as long as we can continue to operate. Under normal conditions, we can predict with high accuracy what the outcomes are going to be. So we want to be looking forward. The analogy I like to give is like, try driving home by looking in the rearview mirror of your car. How far are you going to get? So we don’t want to have metrics that are rearview looking. We want to be looking out the front windshield.
Max Krug 12:17
So if I understand, okay, these are the drivers of my organization, then I can put some I can take some statistics about the process, how it’s performed, and make predictions about the future. And if I first say, I want to understand is that process stable? Is it able to deliver what is necessary?
So we always look at trying to get process stability first. Typically, I see and companies, they’re swimming in problems, and they’re reacting and firefighting all day long. So we need to stop the firefighting. So that’s a reactive mode of operations. We want a proactive mode of operations. So what does that mean? It’s like stop the firefighting. Let’s understand what’s creating the firefighting. And then let’s put process controls in place so that the process doesn’t wander, doesn’t drift.
And if it starts to not create the outputs that we need, we take immediate corrective action. So the first step is always to get process stability. So what that means is, we’re able to understand what the things that have to happen in the process are? What are the inputs to the process, and make sure that they stay within desired limits? So we’re using statistics to make predictions?
Max Krug 13:28
Looking forward, we’re taking process data. And we understand what does normal looks like. As long as things are operating normally, the outcomes are highly predictable. So the first thing is making sure we do things consistently. So it’s inevitable, every company I go into that has a multi-shift operation, the first shift comes in, let’s take a specific machining center, they set up the machine, and second shift comes in, oh, that guy doesn’t know what the heck he’s doing.
He’s got it set up wrong. So he starts making adjustments to the process. And all of a sudden, we start having quality issues. So I see it all the time in companies where people think that they have more knowledge than the other guy, and they start making adjustments, and then the processes start to go out of control. So we want to prevent that from happening, saying, you know what, there’s only one best way to perform the process.
Max Krug 14:22
And SPC helps us to make sure that we’re performing that the best way, and we can see it if something changes. We can immediately react to it before we have a problem that gets you from a reactive mode into a proactive mode. Then once we get stability, now we can focus on capability. Capability means we’re delivering to our customer requirements. So think of the stability.
It’s the voice of the process, saying, okay, what’s the process telling me I’m taking data and the process and I take statistics and say okay, this is what the process is telling me then capabilities. What’s the voice of the customer? So can we make the process the voice of the process match the voice of the customer? Now we got a process of stable and capable, and SPC statistical process control makes sure that we keep those processes operating so that they meet the customer requirement. Okay.
Sam Gupta 15:21
So as an executive, you know, I get all these terms throwing around. And every time I talk to a person, I get a new term. So here you are telling me, SPC. And obviously, I get the picture between forward and backward. But that sounds like more of the predictive or prescriptive analytics. So is there any correlation between AI predictive analytics versus SPC?
Max Krug 15:43
Yes, so SPC is also the same thing, right? Predictive, right. So we want to be able to predict what the outcomes are going to be. So, of course, things are changing all the time. We have different sales. A mix can change within the organization, sales, demand can change, our material supply could change. So there are all these changes happening.
We want to make sure that those changes don’t affect the outcome of the organization. Employees are changing. So it’s a way to make sure that giving all the variables that can happen in the organization, that it’s still able to deliver what’s needed to the customer. And I’m talking the external customer, but also internal between process, that’s
Sam Gupta 16:23
Okay, so tell me a story of a customer where you have worked. So tell me the state where they were in? And then what work did you do for them? And then what was the impact because of that, because I’m actually trying to relate to what SPC really is, to be honest, okay, I don’t know if it is going to be a tool that I need to get in my organization.
So tell me a story where you have implemented this, and, and walk me through the history of the organization, give me details about what the organization was, what was their industrial products, you know, what they were manufacturing, and then the kind of work you did, and the results as well.
Max Krug 17:02
Okay, so I helped the company put it in statistical process control. They asked me to come in. They were having trouble with late deliveries for customers, high scrap levels, high reject levels, high rework, rework levels. And so they’re like, we’ve tried all these different things to try to improve, and we’re not getting any better.
I said, Okay, let’s talk about statistical process control and how we use that to help you get better. So again, using the Pareto principle, I would say 80% of their scrap is coming from 20% of their processes. So if we can focus on that 20% of the processes, and they were a company that was a powdered metal manufacturer, so they supply the lawn and garden industry.
Max Krug 17:47
So they do components for lawnmowers, snowblowers, that type of equipment that they’re supplying the OEM. And so they were having trouble. And so we started to look at, okay, their molding process. So if you’re familiar with powdered metal, they take metal that’s in a powder form, they compress it in a press, they run it through a sintering oven, they do some secondary machining and maybe some other processing in terms of heat treating, or plating and send to the customer.
So the molding process was the process that was giving them most of the problem. Of course, they were finding the defects downstream, right? It’s like, oh, after it’s centered, oh, these parts are out of spec. Right? So is it the sintering oven that’s causing the problem, or some of this stuff was filed after machining? Where’s the problem? So what we did is we said, You know what, it’s really back in your molding department that’s creating most of this problem.
Max Krug 18:35
That’s what we started, say, Okay, let’s see if we can put some statistical process control in the molding department. They looked at the parts and said, Okay, again, if we look at all the variables in the process, again, I would say 20% of the variables are creating 80% of the good quality. So we get to understand what variables are controlling the process. That’s where we want to put SPC in place.
So when we did the analysis, we found that the weight of the product had was a good indicator if the process was operating correctly. So if I had too little weight, that means all the features probably work to spec. If I had too much weight, that means maybe some things were oversized, or we had too dense of material. So we started to say, Okay, let’s just start simple. And let’s start capturing the weight of the product coming off the press. We know what normal should look like. We know the tolerances on the weight. So let’s start capturing samples of the process to see how the weight is how consistent it is from cycle to cycle, and from hour to hour, and from shift the shift. So we started collecting that data.
Max Krug 19:44
And I did SPC training for their people. So they understood the concepts of variation, what creates variation, how do we control variation, and again, we don’t need to focus on everything. We just need to focus on those critical few things that are creating the most disruptions. In the output, if we can control the weight that controls a lot of the process, so we started taking data. And it’s funny, because I said, Well, the first thing we need to do is make sure that our measurement system is capable.
So can the measuring devices that you’re using actually measure accurately and precisely? So we did a, we did a gage study and found out that the equipment is it can’t measure precisely and accurately. Okay, so I got to fix that before I start doing SPC because then I don’t know, the variation I’m seeing is it coming from the measurement system are coming from the process itself.
Max Krug 20:39
So we had to correct the measurement system. And we got that under control. Now we can see the variations all coming from the process. So we did the training, we get a software that we use, we started plugging the data. And then it’s like. We want to train the operators to be able to read the SPC chart. If I can’t read the chart, it doesn’t do me any good.
So it’s like having a roadmap. And I look at the roadmap. If I can’t read the roadmap, I gotta get to my destination. Yeah, I can’t. So the SPC is the voice of the process. It tells me what’s happening. If I understand how to read the SPC chart, it gives me information about what’s happening in the process. Now I can understand what’s going on.
And if things start to go out of normal condition, I can take immediate corrective action. So, in this case, their scrap levels came down by 75%. They right there, their delivery performance went up, their customer satisfaction went up less rework, less scrap, right cost savings, so there were huge benefits for the company.
Sam Gupta 21:44
Okay, let me ask you this, let’s say if you’re working with a customer, and it seems like they must have a really sophisticated quality department where they might have several steps in the quality processes, and they must be doing a really good job in tracking the scrap, right? So some of the customers that I work with, I mean, they don’t even track scrap, they don’t even track the rework. Again, I mean that data may not be available in the system.
So typically, would you require an ERP system before you can start the work? Are you going to interview people? How are you going to find out where the most improvement needs to be? Is it going to be just the process starting that you need to do you need to interview people? So tell me a little bit more about which customers are going to be the right fit for SPC?
Max Krug 22:30
Okay, so I run into a situation where they don’t have any data. So I come into that situation, what I do is I go talk to people, the people in the process know, if you talk to the operator, he knows how much scrap is coming off the process, even though we’re not tracking. We don’t need to have super accurate data to get started. Yes, if we have the data, that’s great. But again, all that scrap data collection is backward-looking, right? We want to be forward with anything.
So the SPC helps us look forward. So if we have that data, that’s great. But if we don’t have it, it doesn’t mean you can’t start right. So we just talked to the people in the process. They know what’s going on. And they know what the issues are. That’s just managed us never listened to them. So if we can gather that information to get started, you can see immediate benefits by putting in some simple process controls.
It’s like I said, with a company that does, we measure the weight because the weight is good, the sintering process is going to be good, the machining process is going to be good. We’re going to have a good product at the end. As I said, there are very few variables that actually control the process. So we don’t need to put all these sophisticated systems in place to measure everything everywhere. Use the Pareto principle and say, You know what, 80-20 rule good enough to get started and then focus on improving from there.
Sam Gupta 23:55
Okay, so do you see this being used in volume manufacturing as well? It seems like this must be applicable, more for precision manufacturing, where they are extremely careful about the quality.
Max Krug 24:07
Yes. So it’s interesting because I went into a company, and they were our job shop. And they had all sorts of process control issues, scrap issues, rework, the same issues we talked about. And I said, well, have you thought about doing some process control? They said, well, everything we do is different. I go yes, that’s why it’s called statistical process control, and not statistical product control.
So most manufacturers don’t understand SPC. You start with measuring the product, but that’s not the end game. That’s where you start to understand where is the variation in my process, and I want to make sure that the outputs are good every time we produce the product, but the power of SPC is driving it back to the process.
So, for example, if you do painting, for example, or powder coating or plating, what are the variables that control the thickness of the part and the adhesion? Well, it’s the cleanliness of the part and maybe how well the part is grounded. And also, in electroplating, it’s like my current level and my cleanliness of the part. Well, if I really want to drive it back to the process level, you know what if I took statistics and the concentration of my batch? Then if I maintain that batch concentration within certain limits, the parts have to be clean. So the power is really driving it back to the process level. What statistical process controls 95% of the companies still measure the product to take it to the next step?
You want to drive it back to the process and say, What are the variables that are controlling the process. And if I can maintain controls on those variables, now I’m doing real process control. So it can apply to any process. It doesn’t matter if it’s a machining process, painting process, plating process, heat-treating process. It can be applied to any process.
Sam Gupta 26:05
Okay, so tell me some more stories in different industries. So obviously, you told me about the powdered metal, you told me about the job shop? Tell me where else it could be applicable.
Max Krug 26:15
So easiest is high volume. If you’re high volume, repetitive, so I’d look at organizations as either high volume or job shop. So if you’re high volume, of course, you know, a lot of companies struggle with maintaining consistency of producing the same types of products over and over. So it definitely applies there. Again, we start with doing product, but we want to drive it back to the process, really doesn’t matter what industry. It can apply to any industry.
If you have customers that have high requirements in terms of quality specifications, that’s the best application. So I’m working with companies in the Department of Defense work. I work with companies that are in pharmaceuticals, automotive, or woodworking. So it can apply to any industry.
Sam Gupta 27:04
Okay, so let’s say if I want to start on this journey, right, and obviously, you are talking a lot about processes. But when I think of the processes as an operations guy, I’m thinking of any ERP system. And I don’t know if I need to have those because they are super, super, super expensive systems, right? So do I need to have an ERP or MES in place before I can start SPC? How would these systems talk to each other?
Max Krug 27:36
Okay, so you don’t need to have an MRP system because SPC is more taking data right from the process of someone’s taking measurements right off the process. They’re going to be putting that data. So there’s a bunch of standalone SPC systems that are you can either integrate with the ERP or you can just have them standalone.
So you don’t sort of necessary condition is you don’t need to have an ERP system up and running. And even if you do, right, a lot of companies I see the data and their systems garbage. So we don’t need to have super accurate data. To answer that question, you can start even if you don’t have an ERP system. You can start with a standalone. You need some type of statistical. And you could do it manually. But yeah, manually, then you need someone to collect all that data analysis, it is better to have electronically, so I prefer electronically, but the standalone systems can get you started right away, and they’re not really that expensive, especially for the return on the investment you’re going to get for investing in a system.
Sam Gupta 28:34
Okay, so next, let’s say if I’m the CFO, right? I’m always looking at what are going to be the implications of any of the initiatives. I’m looking at the opportunity cost. So it does seem like that, you know, probability, the customer satisfaction is going to improve, the quality is going to improve, but it seems like we might be adding additional steps to the process. So, if I’m not collecting today, then most likely, I’m actually going to be introducing these new steps. And that is actually going to slow my processes down. Right? So typically, with the SPC initiative, do processes get slowed down because now I’m introducing additional steps. I’m trying to weigh the pros and cons of the initiative. Tell me if there are going to be any new steps in the process if they are going to slow down the process to weigh it against the benefits that it is going to provide for me.
Max Krug 29:28
Yeah, so most times, you’re collecting data in the process now. It’s just putting that into a system that can actually give us feedback on how the process is performing. So if we take a machining operation, the operators doing the check. So whether he’s writing those dimensions down or not, it’s doing the same thing. It’s just capturing that data, and there are systems that you can actually connect Bluetooth with the gauge to the data collection, and you take measurements like you’re doing, and it automatically collects that data.
So there’s no actual extra effort by the operator to put this data into the system. The benefit is it’s going to give us the feedback and the process immediately. So that’s where we don’t have visibility now. So no extra effort, the benefit of having better visibility and the process. And we don’t want to have inspection-based quality, right. So if you have a bunch of quality tech quality engineers that are going around doing checks periodically, you can reduce that amount of work by having the SPC. So it’s actually gonna free up those resources to provide to do other things for the organization.
Sam Gupta 30:37
Okay, so let me make sure if I understand this, so let’s say if I have a bunch of equipment that is actually doing the quality work, right. And right now, my quality guys, maybe taking the samples from the product, and they might be noting it down. And that’s all they are creating the certificate of compliance. That’s what it’s called, from the quality perspective that some of the customers may require. If the manufacturers have, let’s say, in the pharma space, or in the oil and gas space, right, because they have to make sure that the products that you are providing comply with the quality.
So in most cases, that is going to be just the sampling process that most manufacturers follow. So in this particular case, let’s say if I have multiple pieces of equipment that are actually measuring the quality, so are you telling me that all of this equipment is going to be integrated with the SPC system, and as soon as the product actually goes through that particular process is tab is that going to measure let’s say, we measure the weight, the weight is going to be captured automatically in the SPC system? And then, in the next step, could be, let’s say, measuring the length that is going to be captured automatically in the SPC system?
Max Krug 31:40
Yep, yep, that’s correct. And then your certificate of conformance could be the outcome of all that data for that loss. So if you have like control, you collect that data through all the different process steps. And that’s your data that you’re going to submit with your certificate of conformance to say, Yep, our processes are in control. And here’s the proof that they’re in control.
Sam Gupta 32:01
Okay, but I mean, in my current process, I don’t necessarily measure every single product. But in this particular case, it does seem like that every product is going to go through the quality process. So it does seem like that this is actually going to slow my process down.
Max Krug 32:14
So you don’t need to measure every product. Again, it’s all about focusing on the ones that are causing the most harm. And again, I would say 80% of your quality issues are coming from 20% of your products. So I go into a company, they’ve been working years to improve quality and haven’t got any results. I go and say, well, my assumption is that 80% of your quality issues are going to come from 20% of your product. So what products are giving you the most headache? Oh, it’s this group. I say, Okay, my assumption next is 80% of the quality issues are coming from 20% of the processes.
So I drive back to the process and say, yep, these two processes are creating most of the issue, just like we did with that company saying, you know, what if we can control the weight that controls most of the processes downstream. Now let’s go there focus and say, okay, what are the variables that are creating the most issue, and if we could put some controls around them, let’s start there. So we started with the weight, significant benefit for the organization. So we don’t need to measure everything. That’s a misconception. We never need to measure the right things. And then measuring the right things, taking that data, and driving improvement from what the data is telling us, then we get breakthrough improvement for the organization.
Sam Gupta 33:26
Okay, so help me understand this a little bit more. Is it going to be more of the temporary initiative that I’m putting in? So let’s say if one of my products is actually giving me the most problem, and obviously, I’m looking at the process, not at the product level, right. So let’s say if there is any specific process there, which I suspect may be the cause of the problem in the process.
I can put my SPC system down at that step and see how that process step is performing. And as I get more data then am I going to get insights that, you know, what are the opportunities for improvement? And once I actually have the improvement done? Can I take the SPC system out? Can you tell me a bit more about that?
Max Krug 34:06
So the frequency that you want to take measurements and how long you want to measure is all a function of how capable the processes so there’s a measurement called CPK. That measures process capability. And depending on what that data is telling us, it tells us the frequency and how often we should take the measurements. Yes, we want to make sure that long term, the process stays capable.
But I’m a proponent of Dr. Deming was. Most of my training came through Dr. Deming’s teaching, and the original premise was to not do the same frequency and measurement all the time. It’s like let the process tell you what’s the capability and adjust the frequency of how often we do measurements based on the capability. So even with the company that did the powdered metal, the frequency of measurement wasn’t the same on every product.
Some products run much better than others. So we reduce its frequency, I noticed because we know the process is much more stable. And we want to push for quality at the source. So we want to have the operators give them the tools to be able to make the right decisions. I don’t need to have a quality engineer or a quality tech come to make the decision for the operator. I want to push that decision-making to the operator and give him the tools to make the right decisions.
Sam Gupta 35:23
Okay, amazing. That’s it for today. Max, do you have any last-minute closing thoughts, by any chance?
Max Krug 35:28
So I think a lot of companies think that SPC is a complex thing that we need to consider. It’s not. It’s really simple once you understand it. The biggest benefit of SPC is the two issues I see in companies. People make adjustments to the process when they shouldn’t, and they don’t make adjustments when they should. Okay. SPC will help solve those two problems. Leave the process alone if it’s operated correctly, and understand what I should take operator intervention to make adjustments and quality will improve significantly just doing those two things.
Sam Gupta 36:04
Right. Thank you so much for your time, Max. This has been a fun conversation. I totally enjoyed it.
Max Krug 36:08
Great. Appreciate your time.
Sam Gupta 36:10
I cannot thank our guests enough for coming on the show for sharing their knowledge and journey. I always pick up learnings from our guests, and hopefully, you learn something deeply. If you want to learn more about Max, head over to futurestateengineering.com. Links and more information will also be available in the show notes.
If anything in this podcast resonated with you and your business, you might want to check other related episodes, including the interview with Jason Chester, where he discussed the challenges today’s manufacturers face with changing consumer behavior. Also, in the interview with Dave Griffith, where he discusses why manufacturers must look for low-hanging fruits when exploring the path of industry 4.0.
Also, don’t forget to subscribe and spread the word among folks with similar backgrounds. If you have any questions or comments about the show, please review and rate us on your favorite podcasting platform or DM me on any social channels. I’ll try my best to respond personally and make sure you get out.
Thank you, and I hope to get you on the next episode of the WBS podcast.
Outro 37:13
Thank you for listening to another episode of The WBS podcast. Be sure to subscribe on your favorite podcasting platform, so you never miss an episode. For more information on growth strategies for SMBs using ERP and digital transformation, check out our community at wbs.rocks. We’ll see you next time.