Last Updated on November 27, 2023 by Sam Gupta
In this episode, we have our guest Chris Harris, who discusses the importance of shop floor data collection for manufacturers. He also provides insights into how every machine has a story and how much you can learn from these stories by collecting and analyzing data. Finally, we discussed the nuances of digital twin and how that could help manufacturing maintenance departments become proactive and efficient.
Chapter Markers
- [0:25] Intro
- [2:58] Personal journey and current focus
- [3:43] Perspective on growth
- [4:09] Pulp and paper industries’ shop floor layout
- [5:21] Shop floor data collection
- [7:50] Your competitive advantage with shop floor data collection
- [8:57] Shop floor scrap handling
- [13:57] Recommended approach to shop floor data collection
- [19:59] The core challenges of a maintenance department
- [27:50] The implementation challenges of a digital twin
- [31:16] Closing thoughts
- [32:14] Outro
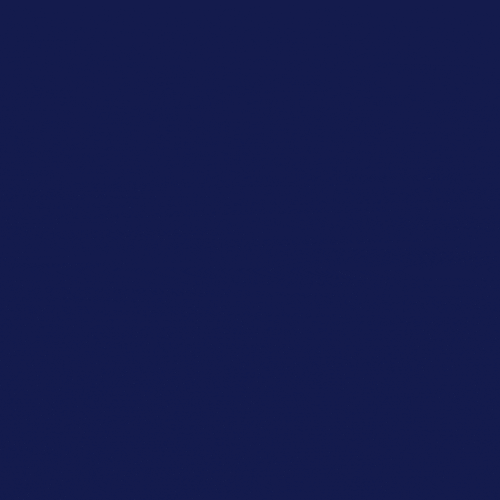
Key Takeaways
- It was that 80-20 rule. We’ve got so many other problems that cost so much more money and our business that scrap is not considered one of the high ends. And now, to have a green economy to have less of a carbon footprint, scrap is stuff that is considered. But some industries, more than others, are more reluctant to identify that, but everybody’s starting to do that.
- None of their problems are easily tended to because they don’t know what the problem is, they know there is a problem. They even may know that what the problem is, but to be able to take charge of what is required to fix it take more of an in-depth shop floor data collection.
- Everyone wants a widget that fixes everything. But no one wants to hear that everything needs to be looked at and analyzed individually.
- Shop floor data collection thus far has been strictly relatable to the machinery aspect. What is the status of the machine, and is that shop floor data collection is done by physically tying it into the machine? Or it’s when a supervisor sits down at the end of the shift and thinks about what happened?
Subscribe and Review
Apple | Spotify | Stitcher | Google Podcasts | Deezer | Player FM | Castbox
About Chris
Chris Harris is a mentor, coach, entrepreneur, process industry veteran, and patent holder. Following a twenty-year engineering and installation career at a custom conveyor manufacturer, he founded and continuously enhanced WPR Services. The company’s primary product is a suite of hardware and software, including vision and voice-enabled devices and connected devices that assist customers in addressing, solving, and planning for various challenges in today’s manufacturing environment.
Resources
Full Transcript
Chris Harris 0:00
Yeah, what are you going to do with the digital twin now that you have a digital twin? What are you doing with it? And how is it adapting? How is it used? So that’s more than half of the battle having all of these data gathered, and every manufacturer that makes Electronics has a wireless way of connecting to so many different things. So now, I have this thing that I’m calling a digital twin. What am I gonna do with it?
Intro 0:25
Growing a business requires a holistic approach that extends beyond sales and marketing. This approach needs alignment among people, processes, and technologies. So if you’re a business owner, operations, or finance leader looking to learn growth strategies from your peers and competitors, you’re tuned into the right podcast. Welcome to the WBS podcast, where scalable growth using business systems is our number one priority. Now, here is your host, Sam Gupta.
Sam Gupta 1:01
Hey everyone, welcome back to another episode of The WBS podcast. I’m Sam Gupta, your host, and principal consultant at a digital transformation consulting firm, ElevatIQ.
Digital twin has been around for a long time. But is it just marketing hype? Is it just a fancy term for shop floor data collection? What are the core challenges digital twin solves? Is it supposed to help overworked maintenance departments and extract stories from each machine? Could it help in reducing waste and improving product quality? These are the questions you will have if you are in the process of exploring a digital twin for your organization.
In today’s episode, we have our guest, Chris, who discusses the importance of shop floor data collection for manufacturers. He also provides insight into how every machine has a story and how much you can learn from these stories by collecting and analyzing data. Finally, we discuss the nuances of a digital twin and how that could help manufacturing maintenance departments become proactive and efficient. Let me introduce this to you.
Sam Gupta 2:11
Chris Harris is a mentor coach, entrepreneur, process industry veteran, and patent holder following the 20 years engineering and installation career at a custom conveyor manufacturer he founded and continuously at WPR Services, the company’s primary product is a suite of hardware and software, including vision and voice-enabled devices and connected devices that assist customers in addressing, solving and planning for various challenges in today’s manufacturing environment. With that, let’s get to the conversation. Hey, Chris, welcome to the show.
Chris Harris 2:54
Thanks, Sam. Thank you very much. Appreciate your time and ability to talk here.
Sam Gupta 2:58
Of course, and we’re super excited to have you. Just to kick things off, do you want to start with your personal story and your current focus?
Chris Harris 3:06
Yeah, I’ve got 25 plus years of experience in manufacturing. We were a conveyor manufacturer. And I got to install equipment in a variety of demographics, as well as industries, and learn from that and created a product line today that is in retrospect of what I learned as a road warrior. And somebody they’re in a factory without how to handle the shop floor data collection that’s needed for manufacturers.
Sam Gupta 3:33
Okay, amazing, so obviously, we are going to be digging a lot into the shop floor data collection aspect and how we can make the shop floor more intelligent than we commonly see in the manufacturing world.
Chris Harris 3:43
But before we do that, we have a standard question for every single guest that comes on to the show. And that is going to be your perspective on growth. Chris, what does growth mean to you? Growth means me the ability to expand not only what I’m trying to do with my products but also the shop floor data collection techniques that I’ve started with and put forward to how shop floor data collection is done. And that would be a good growth platform.
Sam Gupta 4:09
Okay, so let’s talk about some of the industries where we were discussing in the pre-show. Chris, you have done a lot of work, let’s say in the pulp and paper and the corrugated box. So tell us a little bit about how these shop floors are for these industries, what you have seen in the other industries.
Chris Harris 4:31
Yeah, and the shop floor data collection thus far has been strictly relatable to the machinery aspect. What is the status of the machine, and is that shop floor data collection is done by physically tying into the machine, or it’s when a supervisor sits down at the end of the shift and thinks about what happened?
And so what I’m trying to do in my industry is make the shop floor data collection be inclusive of everything about a machine center. And so when we’re learning about the success of a production line, we want to understand what created that success and the aspects of everybody who touches the production, whether it be a maintenance, person quality control, who’s looking, trying to get all of that information out of one platform into the decision-makers to analyze that.
Sam Gupta 5:21
okay, so when we look at shop floor data collection, obviously, shop floor data collection could mean a lot of things to different audiences. So here, I believe that you are talking about slightly more operational data and the shop floor data as the product is moving through the production line, and you are talking about shop floor data collection directly from the machine as opposed to inputting this data.
Let’s say in some sort of ERP system, or whatever system they might have on the shop floor to be able to gather this data. So tell us a little bit more about what shop floor data collection means to you. And why is it different from what manufacturers may be doing at this point in time on their shop floors?
Chris Harris 5:59
Yeah, so the shop floor data collection for me has always been to be a wedge and to bridge into an ERP. So many software’s out there for a production facility are done from the outside into the machine, and I’m taking the whole idea from the inside of the machine and working back into the front side, a lot of that sales on the front end, and databases that are empty, ideas that we in a perfect world want to get all this data.
And I’m coming at it going here this data is possible to get this does not or here’s how the data needs to be shaped through then your platform your ERP system can take and do this magic that it says to do so looking again from the inside out and in creating the unicorn of the pull versus push and how do you run manufacturing and pulling versus pushing and so creating that environment and ERPs now go to the sales where the 20 years ago that wasn’t it, they were just production It was a loose connection to a sales platform, and I’m trying to feed all of that.
Sam Gupta 7:07
Okay, amazing. So So tell us some stories where you have done some work tell us the prior state of the shop floor, what kind of work you have done, what were the benefits of the work that you have done, and how that translated, let’s say, into either the revenue or business growth.
Chris Harris 7:25
Business growth that I’ve got is has been understanding how to build my product and listening to what is needed, so I’ve gotten a lot of sales inquiries for not necessarily a product, here’s a device, and you use it, and you do it I’m coming in with an idea, and that idea is shaped from what are the needs the customer has at that moment.
Sam Gupta 7:50
Okay, so tell us how you have helped some of the customers so customers or you might have some sort of stories where you saw a situation where they could have used shop floor data collection as they’re either a competitive advantage or maybe to reduce the costs or to improve their products.
Chris Harris 8:05
So tell us some of these stories from that perspective shop floor data collection with the material it seems to be raw material usage and scrap those from manufacturing those are the data is the primary data is that every manufacturing process is wanting to do reduce scrap make the most out of the raw materials and then ship something and so data has been limited to just that type of thing.
I’m trying to grab data for other departments, not just production or other plus saving revenue avenues in just raw material and scrap and then ship product and so how can I have a platform that is able to implement it and be able to touch all of the different departments to justify our allies in a variety of ways.
Sam Gupta 8:57
So okay, so many talks about this scrap, right? Is this a scrap problem going to be on every manufacturing shop floor, or is it limited to some shop floors?
Chris Harris 9:09
I mean, you got somebody in a CNC mill shop is putting scrap metal pieces all around for based on how they’re doing a pass of their CNC work. So there’s a lot of facilities that have scrap pizza dough. I worked in a facility that was just sweeping pizza dough off the floor. And so I’ve seen a with working with conveyor and conveying material from one side of the plant the entry of raw material and the exit of finished goods.
I’ve seen that there are a lot of parallels with wanting to do scrap and because a lot of industries do that. Other industries say let’s make our business model on reducing waste and whatever that is and making the most out of the materials that we have coming in.
Sam Gupta 9:56
So in your experience, let’s say if you talk about scrap. In my experience, a lot of manufacturers don’t even track that sometimes they are simply going to have scrap as the production output. They don’t even do the production casting. So how are they going to know how much space they are producing?
Chris Harris 10:13
So in your experience, do manufacturers practice scrap? Always? If not, what can they do to reduce the scrap? It’s not been a concern because it wasn’t known to be a concern until you started really doing finite analysis of your manufacturing process 20-30 years ago that it was discussed.
But it was that 80-20 rule. We’ve got so many other problems that cost so much more money and our business that scrap is not considered one of the high ends. And now, to have a green economy to have less of a carbon footprint, scrap is stuff that is considered. But some industries, more than others, are more reluctant to identify that, but everybody’s starting to do that.
Chris Harris 10:57
Because the shop floor data collection is easier to get, there are too many tools. There are so many tools that you can gather data that allow you to then validate that 20% of the stuff I didn’t think is needed. I can go grab that now. And again, the benefits of reducing waste, just waste handling waste, don’t waste away.
And knowing that you have so much in some industries may say you know what, we’re running 40% waste, we’re not getting any better than this. So then be creative on how to use that waste to do something else. And so there’s the analysis that’s being done, slowly but surely, that you see in the news? Oh, you’re finding more. You see more and more on the news.
Sam Gupta 11:35
Okay, amazing. So when you talk about this green economy concept, there are some regulatory agencies as well that are monitoring. So I don’t know if there is going to be any penalty or reporting required by the manufacturers if they are reducing the waste or not. Have you seen any of that by any chance, from the government agencies for manufacturers to be able to report the waste and what they are doing to reduce the waste in their facility?
Chris Harris 12:01
No, I haven’t. I don’t have any data on that. WPR is my product that has the ability to gather data, whether that be a metric, and the number of this, or the size of that. And so, the tools that I’m gathering are able to take and quantify that metric that’s needed.
Sam Gupta 12:21
Okay, amazing. So you spoke about finite analysis, and some of my audience may not be familiar with what finite analysis is. So tell us a little bit more about finite analysis and how that is relevant for manufacturers. And if you have any stories where they were not using finite analysis before, and maybe they started using afterward, what was the impact of using finite analysis.
Chris Harris 12:42
The Finite analysis is really just meaning that people can look into things a little bit more depth. So my reference to finite analysis was the path I was trying to deliver the message. So again, analyzing things one or two steps further and analyzing things with the answers that your original analysis creates, and so finite, then it has to do with the tools to be able to analyze that the computation of power to analyze that there that allow you to use words like the finite analysis.
Sam Gupta 13:18
Okay, so, give me some examples. So let’s say if I was not using finite analysis before, and maybe I did not have enough depth, but now I may be using finite analysis, and maybe I’m going to have depth. So let’s say if I’m the pulp manufacturer here, Chris, okay. And I am trying to take advantage of finite analysis on my shop floor. So what kind of insight. Am I going to get on the shop floor that I did not have before more data?
Chris Harris 13:40
Again, the finite and now the in-depth analysis is thinking about more ways of shop floor data collection? Again, is there additional data? We don’t know.
Sam Gupta 13:57
Okay, so tell us some of the challenges that you have seen in these industries when you are doing, let’s say, shop floor data collection. Okay, what are some of the challenges of do you find that the machines that you are interfacing with? Are they modern enough to be able to get the data from those machines? What kind of preparation is required? Do we need to upgrade the machines? Do we need to put any sort of sensors before we can get the data from the machines?
So let’s say if I take you to a manufacturing shop floor, what would be your approach recommendation, the steps that you are going to take in order to get the appropriate data that you need to be able to provide the insight to be able to grow the business?
Chris Harris 14:34
Yeah, every machine has a story to tell every factory floor has a story to tell all around the machine from raw materials in effort out, and cameras and audio data gathering from those two can extrapolate that data. A lot of people are taking an old machine that is mechanically inclined to run production but doesn’t think that you can update its technology of telling a story to get to a device because of primitive ways of running a machine.
But every machine has a baseline story and can tell you something you didn’t know yesterday. And with having the ability to gather more than one bit of information from a machine, now the machine tells you the story that you need and then tells you whether or not you really need to get a new machine and tells you if you really need to upgrade controls. But it starts with knowing what the root cause is? And what is it that we’re trying to fit?
Sam Gupta 15:39
Okay, so you mentioned that every machine has a story to tell. So tell us one story. And probably the last machine that you interfaced with that rocked your world completely, that was really fascinating for you to be able to find that you probably were not expecting when you started your process.
Chris Harris 15:58
The viscosity of the liquid. The temperature of the viscosity of a liquid. And how temperature and pressure affected glue, and how it was the thing that never was considered to then revolutionize the ability to glue in the boxing industry that was really unique. The other unique thing found is a bug zapper that was affecting laser LIDAR or laser pathway sensors that a handful of different companies make some of the electronics manufacturers, but obscure scenarios that you don’t know unless you’re analyzing a lot of things from the outside looking in.
Sam Gupta 16:45
Okay, so this is very interesting. And I’m super fascinated about this particular story where you are talking about the viscosity and temperature, and that is affecting the group process. So what was the original expectation of the shop floor when they did not have this insight, and then you started gathering the insight?
And then they came to know that there is something going on here that I did not know, and I got to know this only because of this shop floor data collection. So tell us a little bit about the situation before in terms of what was the insight that existed or the myths that exist around the shop floor and how that changed once you find this insight from your shop floor data collection process.
Chris Harris 17:24
Good luck not to see data that is changing. When you’re charting data, the inconsistent things are visibly there, more so than the consistent thing. Those ROIs allow you to see similarities and not similarities.
And so that tying into a variety of sensors that are existing, or tying into a maintenance technician who said I do this 17 times, and I always go to find this data out and then I go home because I know what that data is to tap into that and then to build trends and tendencies from that. And the data have shown that you can analyze quickly then allow you to allow me to come up with that let just because it was a variable that changed a lot that I didn’t know that you don’t know.
Sam Gupta 18:18
Yeah, so every story has some sort of trigger, right? I mean, the story starts from somewhere. So in this particular case, what was the original trigger? What were the core problems that the shop floor was having? And then probably you were brought in, or your team was brought in, or somebody was brought in that you knew. So what was the trigger?
Chris Harris 18:36
The problem was that they didn’t know that they were looking, they wanted to know, a factory goes through a new maintenance manager who tries something new, a new production manager does something different, a quality person who just attended some seminar that said, this is the buzzword that we’re supposed to use for our game, our thought process in our department of this year.
And so none of it was working because they’re all still changing. And so that trigger was how we’re going to get the data we don’t know to help us, we don’t know, and how to how do we get that data. That’s where my wedge data gatherers come into play. When you said none of it was working, so I want to dig a little deeper on that. So what was not working? The product quality wasn’t good enough. The efficiency wasn’t there.
Chris Harris 19:22
What were the problems? Now working is a harsh term. It could be more optimized. It could be better. There was always the challenge to get that extra 20% in the 80-20. No. And so, it wasn’t always a perfect thing.
So I learned from seeing lots of maintenance departments and seeing how maintenance works to see how production interacts with the production employees, production managers, and employees and seeing the need for all these things that are different. But the fact is that you need to gather the data, somehow raw machine metrics, and people met.
Sam Gupta 19:59
Great. So let’s talk about the maintenance department. So what are the core challenges that you typically see in a maintenance department that you have worked with? What are the core challenges?
Chris Harris 20:11
I have seen every maintenance department were overworked and underpaid, and we just had an employee quit? And the efficiency of our department just went to 75%, because we’ve lost one out of four. That’s a very real number. And now that three other maintenance, people have to take that other 25% without a pay increase, and now you have a moral issue.
And so those are the things that I’ve seen in maintenance departments. So why are the older work? What are the core reasons? Why are the award-winning is the there’s not money put in for budgets, there’s not there’s a maintenance that said, hey, we need to this money. After that, may I talk earlier about a different maintenance manager who has ideas and educated ideas from a college or from life experiences that they’ve gathered in, but everything costs money, and money’s not spent the maintenance, because 80% of maintenance is reactive?
And so companies know, maintenance can be a very expensive challenge. But 80% of it is reactive, and the latest people are just trying to get on the flip side of that to not have to become too reactive. So that’s the thing that I’ve seen with maintenance departments.
Sam Gupta 21:31
So obviously, when you talk from the CFO perspective and let’s say if I take the side of my manufacturing CFO, they have a lot of competing priorities, right? So from the CFOs perspective, or CEO’s perspective, maintenance, people are saying that I have tons of problems with my service, people are saying they have tons of problem production, people are saying they have tons of problems.
And marketing, people are saying they have tons of problems. So it’s not easy for a CFO to think about that. So in your experience, let’s say if you were to make some recommendations to a CFO, and again, the goal of this exercise is going to be to create some sort of ROI, so that whatever I’m spending today, either I can spend less. That’s what CFOs care for.
Chris Harris 22:11
You just said it. The CFO hears from the quality department. I have problems in every department. So I’m coming in from a product to understand that every one of those people has problems, but none of their problems are easily tended to because they don’t know what the problem is, they know there is a problem.
They even may know that what the problem is, but to be able to take charge of what is required to fix it take more of an in-depth shop floor data collection. And that’s where I’m coming in is tying into each of these departments and being able to get the data to take the pains away from that person. And it starts with talking to that person and cleaning and inquiring off of them the data that’s needed to make his life better than ultimately CFOs life.
Chris Harris 23:00
Okay, so when we talk about the maintenance, and I’m actually going to give you an example, right, so let’s say if I’m driving a car, and if I look at the maintenance, from the cars perspective, typically you are going to require a lot more maintenance and an old car, right. And this is what I see on the shop floors as well.
Whether you talk about ERP systems, you talk about the machine. Each of them is some sort of machine, right. So the reason why you would require a lot more maintenance in these machines is that they are probably too outdated. Right, and they are not getting things. They have fewer things, all machines have fewer things, they have fewer electronics, and new machines have lots of new electronics that then require new maintenance technicians to be able to attend to them.
Chris Harris 23:48
So yeah, there’s, they’re newer things. And they’re easier to obtain. And they’re easier to build. But they also add complexity to the whole process because they are new things. New things don’t always work out. And there’s another new thing that replaces the new thing. So when they put machines together, they really had to think what’s the simplistic way to do this.
So I see Emerson, both as a former machine builder and the company, we were making robotics and conveyor and other machinery. I’ve seen the migration with new stuff, old stuff, and I’m 50-50 based on the situation every situation is different. And knowing the analysis that needs to be done tells you whether or not you’re on this side of the 50 or that side of the 50. And those are things that my product can do ahead of time to justify how a machine performs. What’s the problem?
Chris Harris 24:40
What’s the root cause? Is it that I spit that the machine is broken down and the four operators hurt their foot because they kick it because they’re mad that the machine is broken down and always because it’s a mechanical nightmare because maintenance spends too much money on it, and we have technicians from the OEM that doesn’t exist anymore.
So you’ve got to analyze and look at it. And everyone wants a widget that fixes everything. But no one wants to hear that everything needs to be looked at and analyzed individually. But it does. And that’s where my tools come in, that allows you to do that to take on that individualized entity, that that machine interaction with a person operating, it has to be able to say whether or not a norm.
Sam Gupta 25:29
So tell us some of the examples or the stories of that 50-50, in which situations the new machine is going to be the right fit, and in which situations, the old machine may be okay. Do you have any stories or examples, or criteria that you would recommend?
Chris Harris 25:46
Not a story, conversations, and it comes down to where everybody knows what data that they want to gather to get that answer. But they have to speculate on a lot of the answers because it’s too hard to gather the data, or that employee doesn’t have time to gather the data.
And so, therefore, if decisions are made, wrong decisions are made because the assumption is maybe that this is a bottleneck for maintenance because they remember last week maintenance guy said the machine broke down.
So they immediately think, wow, my machines always broke down. But that may have been the only time it was broken down in 10 years, but that person remembers that and then makes an ill decision based on that. And that’s why qualifying the data is an important part of it.
Sam Gupta 26:35
Okay, amazing, and so so from the maintenance perspective, what other stories or recommendations that you might have, or maybe you have some other stories from the maintenance perspective that you would like to cover?
Chris Harris 26:45
Yeah, that’s not a product that I sell. Unless selling smiles is a product is the most important thing. The most important thing with the maintenance department is morale. And as a vendor, if I’m involved with it, I’m going to try to get a chuckle and try to take and try to create that because I’ve seen the success of good maintenance type. And how can you take him and leave the main shop and give the main his department the tools that they need and the data that they need to then make an informed action or decision based on that?
So that’s what I’m trying to do. But then it also goes in production and the folks producing. So, for instance, I did a report. And when we put the reporting together, we had no negatives; we had no downtime, not minutes off. Not that everything was uptime, and green and nice fiber colors, and not red and x’s and things like that. So shape your data in a kind way is one of the delivery messages that we want with our data gathered.
Sam Gupta 27:50
Okay, so obviously, you talk a lot about digital twins as well. So let’s talk about the complexity of the digital twin in implementing that. So let’s say find the manufacturer or the manufacturing CFO. Yes, I’ve heard that the digital twin is cool. But I’m looking to see if I can make the life of my maintenance people easier by implementing, let’s say, a digital twin of a machine or a process.
Chris Harris 28:13
In my opinion, a digital twin is a marketing word that, again, was talked about earlier. Offline, people don’t know what a digital twin but they know their competition bought two of them last week. They want to buy one now. They want to buy three now. So digital twin is just knowing the data and having the data pop up in front of you and telling you here it is.
And the digital twin is all of those bits of data that are pertinent. Someone can say I’ve got a digital twin, and I have all data pertinent, but I can’t read any of it. I don’t understand it. I don’t know how to extrapolate it quickly. And so my interpretation of a digital twin is the data that’s needed all readily available there in one page on one period.
Sam Gupta 28:55
Okay, so in your case, you are saying that digital twin is just a marketing term, clearly, the shop floor data collection, if you think about it, so basically from the resultant protected as long as the data is there, on one page, it describes, let’s say whatever trends you’re facing with respect to the machine, and it actually solves the problem.
That’s what you should be looking for. Right? So in your experience, tell us some of the, let’s say, well recommended digital twins. And if I were to implement a digital twin in my manufacturing plant, what are the attributes other than data being on one page, and the data is relevant to my process? What else should I be looking at? In the digital twin?
Chris Harris 29:33
What are you going to do with the digital twin now that you have a digital twin? What are you doing with it? And how is it adapting? How is it used? So that’s more than half of the battle having all of these data gathered, and every manufacturer that makes Electronics has a wireless way of connecting to so many different things. So now I have this thing that I’m calling a digital twin. What are what am I gonna do with that data? So that’s the whole digital twin 2.0.
Sam Gupta 30:02
Okay, amazing. So, that’s it for today. Chris, do you have any last-minute closing thoughts?
Chris Harris 30:06
Some of my challenges with using vision and video and audio, there are people who feel an invasion of privacy with cameras, and the challenge of how to address that has been a subject that I’ve been working with to try to offer up these solutions that help manufacturing environments and bring a lot of smiles to employees faces that then create a really good cohesive work environment.
So the challenges with that if you have any further shows that maybe touch base on that or you got topic or industry experts that know about that, I’d love to be able to participate in something like that.
Sam Gupta 30:44
Okay, amazing. We’ll definitely keep you in mind. And my personal takeaway from this conversation is going to be every machine has a story, and it’s up to you how you want to craft that story using the data. So on that note, I thank you for your time in class. This has been an insightful conversation.
Chris Harris 31:04
Yes, thank you. And it was really very impromptu. I had no idea that I was going to do this, and I would have worn more than a T-shirt for a verbal or audio-only call.
Sam Gupta 31:16
Alright, thank you so much. Thanks. I cannot thank our guests enough for coming to the show for sharing their knowledge and journey. I always pick up learnings from our guests, and hopefully, you learned something new today. If you want to learn more about Chris, head over to WPRServices.net. Links and more information will also be available in the show notes.
If anything in this podcast resonates with you and your business. You might want to check out the related episodes, including the interview with Dave Griffith, who discusses why manufacturers must look for low-hanging fruits when exploring the path of industry 4.0. Also, the interview with Jason Chester, who shares his thoughts on how evolving consumer trends are forcing manufacturers to rethink their approach to managing manufacturing processes.
Sam Gupta 32:14
Also, don’t forget to subscribe and spread the word among folks with similar backgrounds. If you have any questions or comments about the show, please review and rate us on your favorite podcasting platform or DM me on any social channels. I’ll try my best to respond personally and make sure you get help. Thank you, and I hope to get you on the next episode of the WBS podcast.
Outro 32:35
Thank you for listening to another episode of The WBS podcast. Be sure to subscribe on your favorite podcasting platform, so you never miss an episode. For more information on growth strategies for SMBs using ERP and digital transformation, check out our community at wbs.rocks. We’ll see you next time.