Last Updated on March 17, 2025 by Sam Gupta
What is inventory? Inventory can be anything that has a financial value. It can be a product or a service. It is anything and everything that goes on your sales order or purchase order. Now, the second task is to manage your inventory efficiently. Before you know about efficient ERP inventory management best practices, let’s discuss the importance of coded inventory i.e. SKUs.
The Importance of Coded Inventory
So, when you look at your sales order, there will be a bunch of headers and product lines. The product lines are entered by SKUs. The whole idea of SKU is that once you have the ID, you grab the whole product information. You are bundling every single piece of information related to that product under that SKU.
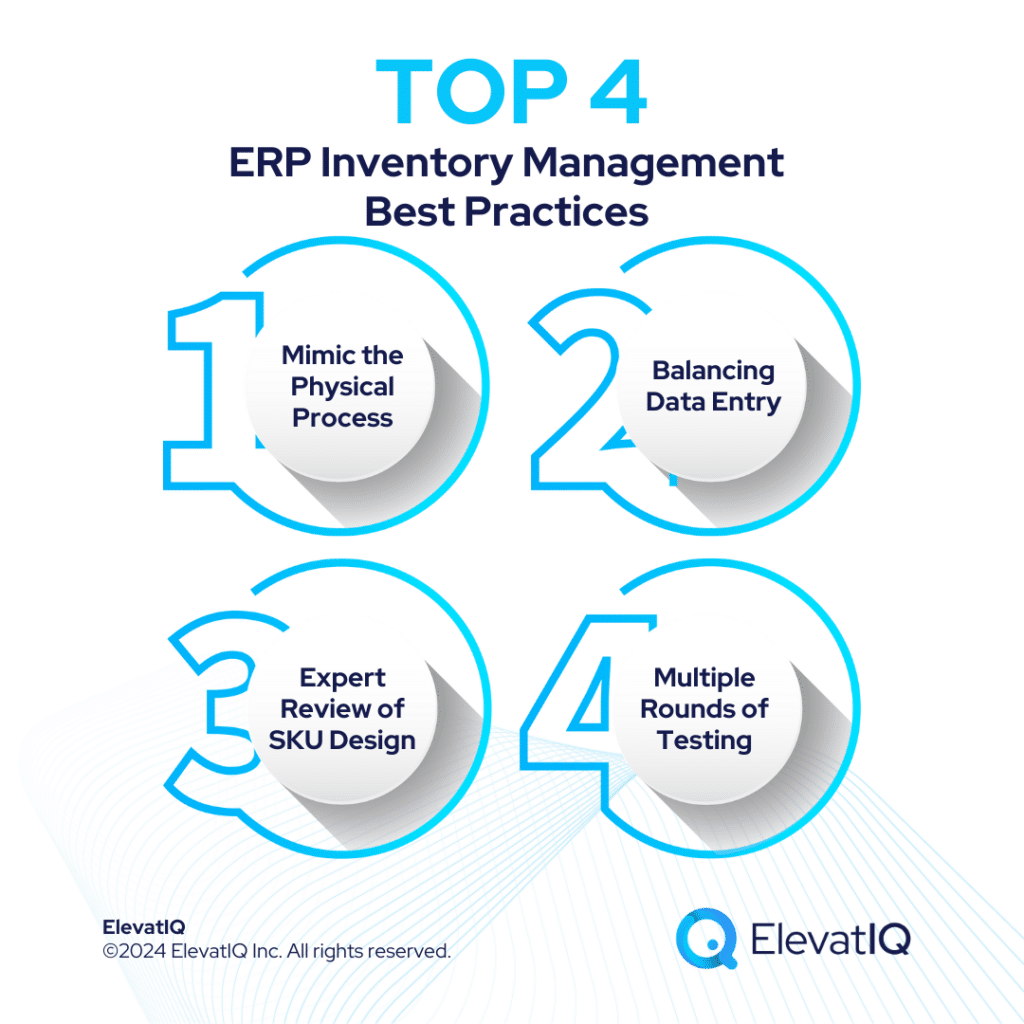
Now, when you look at SKU, obviously there will be SKU numbers along with a lot of different layers. These layers can be either dependent or independent. Let’s understand this with an example. Suppose we have four different SKUs – 1100, 1101, 1102, and 1103 which are independent. Each SKU will further have multiple data points. Suppose the SKU number 1100 has 2000 different data points. What are these data points on the inventory level? These data points are going to be everything that defines that particular inventory, for example, a lot number.
The whole intent of keeping information bundled up is to make sure that your data entry is simplified. Let’s say you want to use this product anywhere in your system or any process. There are going to be 1000 to 2000 data points associated with each SKU. It could be weight, dimension, lot number, or any other attribute related to the product. If you have to enter 2000 different data points, you are going to go crazy. Therefore, you need some sort of description of your inventory that you can grab quickly.
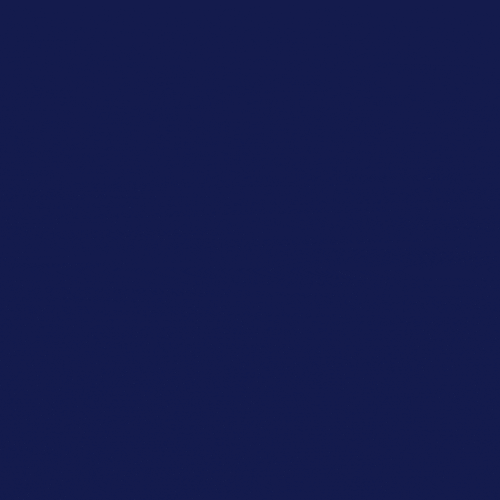
Advanced Inventory Types
The way you model these SKUs defines what result you are going to get out of your ERP. Therefore, product modeling is very critical here. Now that we have cleared the basics, let’s dive into types of inventory. There are three kinds of inventory: dimensional inventory, piece inventory, and matrix inventory. Understanding each of them is important as it will make both your ERP selection and ERP implementation easier. Using an ERP system that does not support any one type of inventory might result in planning issues. It might also result in ad-hoc processes and increased admin effort in correlating dimensions on top of raw data.
1. Matrix Inventory
Let’s understand this concept with an example. Suppose there are two shoes and the only difference in the production perspective between them is the pigment used. One is black and the other is red. The way the manufacturing process works is how you organize the information. You reutilize as much as possible. The more you reutilize, the more financial efficiencies you are going to get from the process. So, these shoes could be manufactured in the same way as all their pieces except when it comes to mixing the pigment. But suppose now you want to change the assembly process for the black shoe.
You have to probably go to every black shoe variant and change this information as the data is not interconnected. This becomes a huge problem in industries like fashion and apparel where the demand is driven by style, season, etc. That’s where matrix inventory comes in handy. The whole intent of matrix inventory is to reutilize the information as much as possible by organizing it differently. As the name suggests it is planned exactly like a matrix.
The base SKU remains the same, but you can have other attributes like color, size, etc related to it. Because of this reason, the data related to the SKU is interconnected. So anytime there is going to be a change in the foundational SKU you are not necessarily going to multiple places and changing that.
2. Dimensional Inventory
The problems and intent of dimensional and matrix inventory are very much similar with few differences. Let’s understand this with two examples. So, whenever you go to a grocery store, you can scan a barcode and it gives all the details of the SKU. Let’s say you have chicken in the meat section of the store. Chicken no. 1 with SKU 1101, chicken no. 2 with SKU 1102, etc. These are very similar chickens with the only difference of the dimension – weight. Now, if the SKU of these chickens is not blended with the dimension weight, you cannot sell it. This is because you need to know this information while packaging when sold and charge the customers accordingly.
Now, for the second example. Let’s say you have a sheet metal and you are trying to cut it into different pieces of different dimensions for car manufacturing. The sheet metal will have an SKU, and so will each of its parts. But just the SKU won’t be enough and you are going to need some sort of attributes to be able to plan at the attribute level. So you are going to create some sort of attribute here, like heat number, and plan the inventory accordingly. It is similar to how the matrix inventory works in the retail industry but won’t have as many permutations and combinations as there are in retail.
3. Piece Inventory
Piece inventory comes in continuation of the dimensional inventory. Let’s take the same example of the sheet metal mentioned above. Now let’s say after entering the dimensions, you need the machine to cut the sheet metal into ten different pieces. But logically the machine can only cut the sheet metal into twelve pieces and not ten. So now, you have to decide what you do with those two pieces. What are the possibilities? One possibility is that you can simply throw it in the scrap. If you throw there is a financial value attached to it, which will make your pieces far more expensive. Another possibility could be you put these two extra pieces for some next job. Now this decision might create friction as it affects the entire production line.
This is where piece inventory should be planned. What do you do with these pieces? How do you organize these pieces? There is a functionality inside ERP in which once pieces are recognized, you have some flexibility in how they will be accounted for. So when you define this nesting process, the system already knows that it is going to create these two extra pieces. So whatever you define in this part of the algorithm, you can define them in advance so that you don’t have to impact your production process.
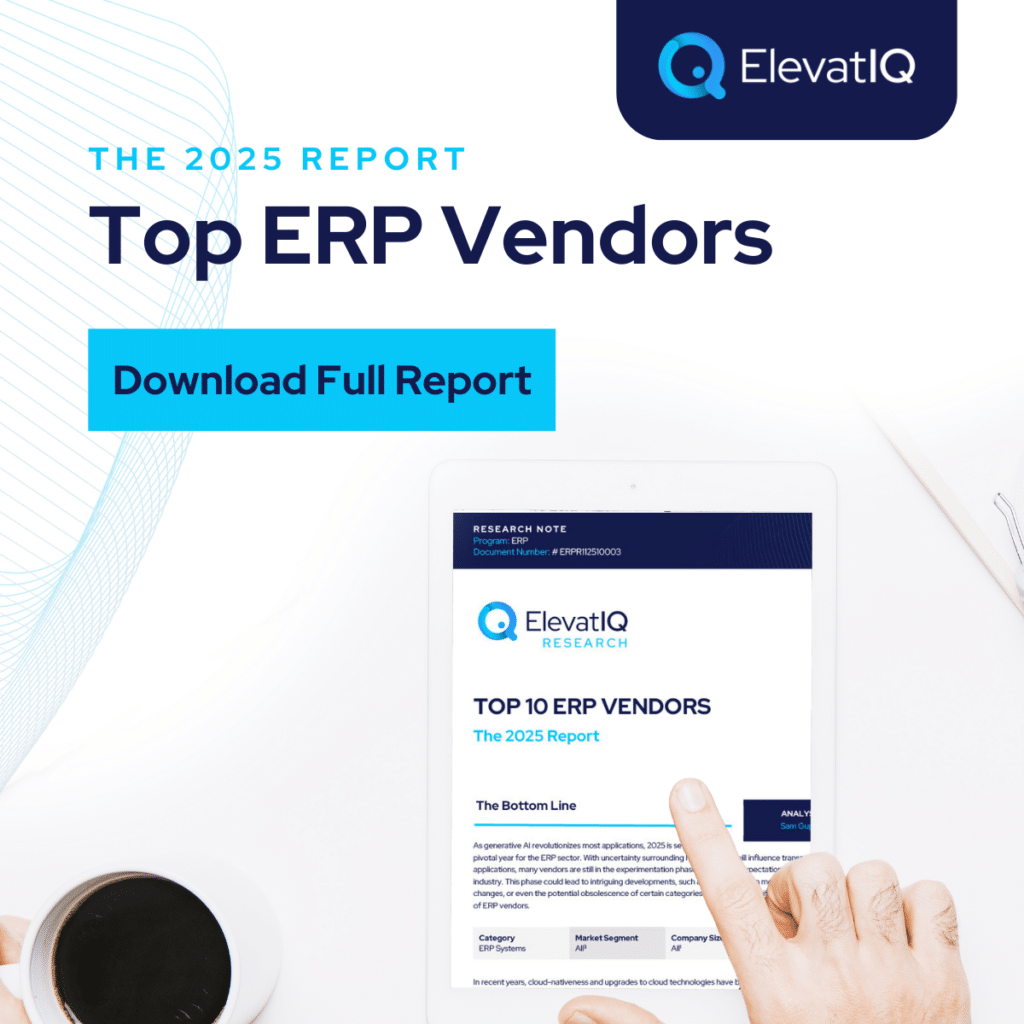
ERP Inventory Management Best Practices
Now that you know the difference between these three types of inventory it will help you design your inventory accordingly. Based on the industry types this will help in devising the ERP inventory management best practices for maximum financial efficiency. Below are the top 4 ERP inventory management best practices that you should always keep in mind before you design your inventory.
1. Mimic The Physical Process
Designing inventory systems that closely mirror the physical manufacturing process is one of the fundamental ERP inventory management best practices. By aligning the digital representation of inventory with its real-world counterpart, you can ensure seamless integration and a more accurate reflection of your operational reality. This strategy involves breaking down the manufacturing process into modular components, just as you would in the physical production of goods.
The goal here is to replicate and optimize the flow of materials and products throughout the entire supply chain. By doing so, you can identify bottlenecks, streamline workflows, and maximize resource utilization. This approach not only enhances efficiency but also minimizes discrepancies between digital records and the actual state of inventory, ultimately leading to more accurate forecasting and planning.
2. Balancing Data Entry
Balancing data entry from the user’s perspective is one of the critical ERP inventory management best practices. It ensures the accuracy and reliability of inventory information. While it’s essential to capture comprehensive data for each inventory item, a balanced approach avoids unnecessary complexity that may arise from overloading the system with redundant information. Prioritizing user-friendly data entry methods not only reduces the risk of errors but also enhances the speed of data input.
You should aim to strike a balance between collecting essential information for effective inventory management and ensuring that the data entry process remains intuitive for users. This strategy helps maintain data accuracy, streamlines processes and facilitates smoother collaboration among your teams involved in inventory management.
3. Expert Review of SKU Design
Engaging independent ERP consultants to review and optimize your SKU design aligned with ERP planning is one of the most effective ERP inventory management best practices. SKU design goes beyond mere identification codes; it involves structuring product information in a way that aligns with the broader goals of the ERP system. Subject matter experts in the field can provide valuable insights into industry best practices, ensuring that SKU design maximizes the capabilities of the ERP platform. This strategy involves considering not only current operational needs but also anticipating future requirements. Through expert review, you can fine-tune your SKU design to enhance scalability, flexibility, and overall adaptability to evolving market demands.
4. Multiple Rounds of Testing During ERP Implementation
Conducting multiple rounds of testing during the ERP implementation is considered crucial as one of the ERP inventory management best practices. This process involves simulating real-world scenarios to ensure that the inventory module functions effectively and aligns with the specific needs of the business. Testing helps identify potential issues, discrepancies, or inefficiencies before the system is fully deployed, reducing the risk of disruptions to day-to-day operations.
Independent ERP consultants play a critical role in this strategy by leveraging their knowledge to anticipate future requirements and forecast potential risks. Rigorous testing not only validates the functionality of the inventory module but also provides valuable insights into system performance, helping you to make informed decisions and adjustments before the ERP system becomes an integral part of your operational infrastructure.
Conclusion
If you are looking to implement ERP inventory management best practices, you must understand the type of inventory you need to design based on your industry. Each of them has its own merits when utilized efficiently for the desired results from the ERP systems. The whole intent here is to figure out what is the best way to organize the SKUs of your inventory. Understanding these concepts will also help reduce manual data entry, which reduces time spent on SKU maintenance and ultimately helps increase the financial margins. This list aims to offer potential options for your further evaluation with independent ERP consultants.
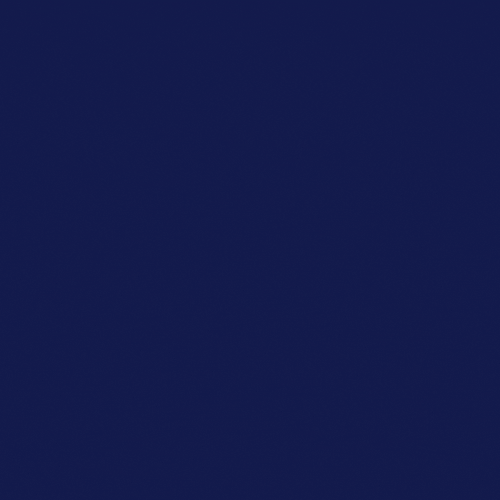