Last Updated on December 28, 2024 by Sam Gupta
Tasked with researching an ERP solution for your manufacturing business? Understanding manufacturing ERP features is the first thing you need. Awareness of their implications is equally critical. While each business needs certain specific features, there are a few common features that most manufacturing companies need, generally offered out of the box with popular manufacturing ERP systems.
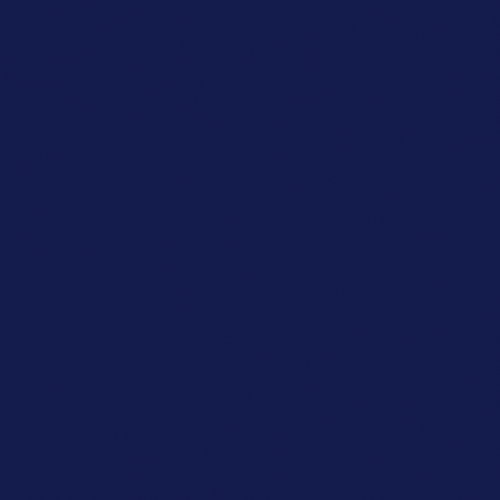
Among manufacturing ERP systems that are likely to contain the most generic manufacturing features, Industry-specific functionality (also known as last mile functionality) is what differentiates ERP products. If you are looking at larger solutions such as Microsoft Dynamics, SAP S/4 HANA, or Oracle ERP products, these last-mile features might be provided by add-ons (built by system integrators) because these products are meant to be slightly technical in nature. The primary audience for these systems is larger companies with higher implementation budgets. Unless you have a very large IT team, your best bet would be to find an industry-specific ERP where most such features (tailored integrations) are provided out of the box for specific industries.
Compared with vanilla systems, manufacturing ERP systems have the natural support for BOM layers, scheduling, and costing, with the ability to report fixed and variable overhead separately for machines and operations. The non-manufacturing ERP, on the other hand, would not have the costing layers, including scalable overhead layers. The manufacturing ERP systems will also likely have features such as replacing a component across all BOMs. Also, features such as swapping out an operation for all BOMs might be limited. Developing such features on vanilla ERP might take forever. The manufacturing ERP, on the other hand, can perform them with one click.
ERP Features for Manufacturers
Manufacturing
The manufacturing features are likely to differ most in ERP systems. While several ERP systems might claim (or pretend) to be manufacturing ERP systems, genuine manufacturing ERP systems typically have a tighter correlation between the materials and operations, as well as the operations and skill sets. These correlations help manufacturing companies have precise control over their operations and reporting.
- Bill of Material (BOM)/Formula
- Material Requirement Planning
- Production Order Management
- Labor and Material reporting through mobile
Finance
- Accounts Receivable (AR)
- Accounts Payable (AP)
- General Ledger (GL)
- Cash Management
- Currency Management
- Multi-entity Accounting (If you have more than one location or entity)
- Fixed Assets
- Tax Management
- Financial Reporting
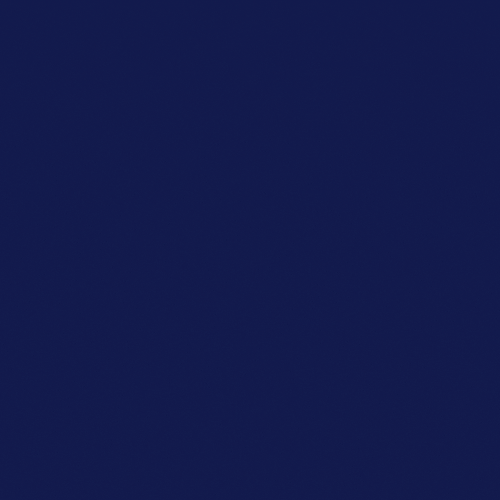
Inventory
- Inventory Management
- Warehouse Management
- Barcode Reading Capabilities
Order Management
- Salas Order Processing
- Purchase Order Processing
- Purchase Approvals
- Customer and Vendor Management
- Pricing and Discount Management
Conclusion
Knowing these standard features and what differentiates ERP solutions is critically important. In order to establish accurate selection criteria as well as priorities. Otherwise, you may end up selecting the wrong ERP product, which typically results in failed implementation and budget overruns.