Top 10 Plastic Extrusion ERP Systems In 2024
Plastic extrusion companies. Used in various industries such as construction, automotive, aerospace, medical, packaging, consumer goods, electronics, and agriculture, they specialize in the manufacturing process called plastic extrusion. Because of its material efficiency, continuous production, and minimal post-processing needs, it differs from other manufacturing companies. The business model could be B2B or B2C. In the case of B2B, it involves large-scale production, long-term contracts, and customization services to meet specific client needs while focusing on cost efficiency and quality assurance.
Plastic extrusion business processes. The process starts by selecting and preparing raw plastic materials, melting and mixing them, and then forcing them through a die to create specific shapes. The next steps are cooling these shapes, cutting them to a length, and applying additional finishing processes. Additionally, effective supply chain and logistics management ensures the smooth flow of materials and finished goods, including inventory management, packaging, and distribution. Regular maintenance of equipment and providing customer support for product customization and after-sales services are also vital to ensure efficient, high-quality production and delivery.
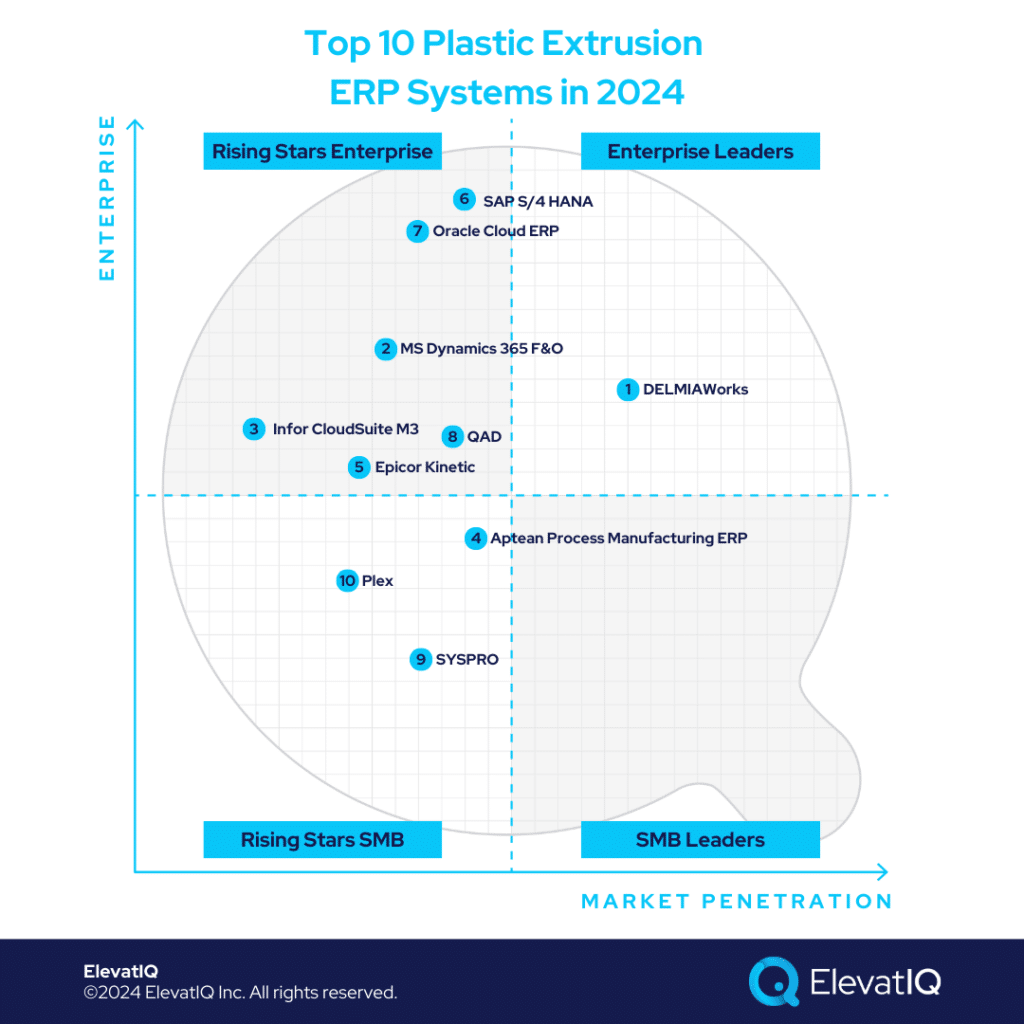
Plastic extrusion ERP needs. Requiring advanced capabilities in inventory management, production planning, and scheduling, and integrated quality control, they need mature capabilities in supply chain management to streamline procurement and logistics. These processes might also be comparatively complex due to the diverse range of raw materials, coordination of multiple extrusion lines, and adaptation to fluctuating order demands. Additionally, handling custom orders requires flexible processes and effective communication, making ERP selection substantially challenging for plastic extrusion companies.
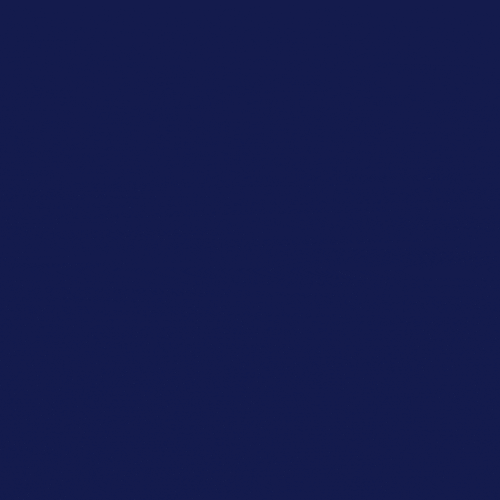
Criteria
- Definition of a plastic extrusion company. They specialize in the manufacturing process called plastic extrusion, used in various industries such as construction, automotive, aerospace, medical, packaging, consumer goods, electronics, and agriculture.
- Overall market share/# of customers. The higher market share among plastic extrusion companies drives higher rankings on this list.
- Ownership/funding. The superior financial position of the ERP vendor leads to higher rankings on this list.
- Quality of development. How modern is the tech stack? How aggressively is the ERP vendor pushing cloud-native functionality for this product? Is the roadmap officially announced? Or uncertain?
- Community/Ecosystem. How vibrant is the community? Social media groups? In-person user groups? Forums?
- Depth of native functionality. Last-mile functionality for specific industries natively built into the product?
- Quality of publicly available product documentation. How well-documented is the product? Is the documentation available publicly? How updated is the demo content available on YouTube?
- Product share and documented commitment. Is the product share reported separately in financial statements if the ERP vendor is public?
- Ability to natively support diversified business models. How diverse is the product in supporting multiple business models in the same product?
- Acquisition strategy aligned with the product: Any recent acquisitions to fill a specific hole for plastic extrusion industries? Any official announcements to integrate recently acquired capabilities?
- User Reviews: How specific are the reviews about this product’s capabilities? How recent and frequent are the reviews?
- Must be an ERP product: Edge products such as HCM, CRM, eCommerce, MES, or accounting solutions that are not fully integrated to support enterprise-wide capabilities are not qualified for this list.
10. Plex
Plex is an excellent choice for plastic extrusion companies, particularly those operating within the Ford or Toyota ecosystems. It adopts a strong MES-first approach, making it a great fit for businesses with highly active shop floors that prioritize Industry 4.0 scenarios. Therefore, plastic suppliers within the automotive ecosystem are likely to find Plex especially appealing. Hence, Plex has secured the #10 spot on our list of top plastic extrusion ERP systems.
Strengths
- MES-first approach. It adopts a MES-first approach, making it an ideal choice for businesses with highly active shop floors and a focus on Industry 4.0 scenarios. It’s particularly well-suited for plastic suppliers within the automotive ecosystem, where the capabilities are likely to be highly valued.
- Stronger automotive last mile compliance capabilities. It offers robust automotive last-mile capabilities that come pre-built, reducing the need for third-party solutions. This ensures that you have comprehensive, ready-made street capabilities that might require additional vendors with other systems.
- Cloud-native​. They started as a cloud-native platform, so the experience is likely to be superior.
Weaknesses
- Weaker plastic-centric core product and scheduling layers. The plastic industry has unique complexities, particularly in process manufacturing. While some products gain wide adoption for covering plastic-centric processes, these processes often present complications, especially with formulation recipes. Although issues like catch weight may be less prevalent, other typical process manufacturing challenges still arise. While certain systems like Plex tailor and enhance other industry processes, plastic-centric processes may lack some detail.
- Not as scalable for diverse business models. It is less scalable for diverse business models, and if your business falls outside the automotive sector, you may encounter challenges despite claims of supporting mixed-mode manufacturing.
- Not as well adopted among plastic extrusion companies​. Plastic extrusion companies adopt it less widely. While they do have some clients in this sector, their presence isn’t as strong as that of other systems on the list.
9. SYSPRO
Plastic extrusion companies outgrowing QuickBooks and needing a more robust solution find SYSPRO well-suited. These companies are typically looking for a smaller ERP system that provides end-to-end traceability within a single country. SYSPRO offers a solution that includes both discrete and process manufacturing capabilities, making it ideal for handling complex business models. Thus, SYSPRO secures the #9 spot on our list of top plastic extrusion ERP systems.
Strengths
- Complex inventory layers. In the plastics industry, inventory management is complex due to various product attributes integral to supply chain and scheduling planning. Some systems may struggle with this, but SYSPRO handles these challenges well, making it an ideal choice.
- Formulation and recipe support. The product has natively built formulation and recipe support.
- Discrete and process manufacturing in one solution. SYSPRO has both discrete and process manufacturing natively built into one solution.
Weaknesses
- Complex plastic extrusion capabilities such as scheduling. Products specifically focused on plastics provide more detailed coverage of complex processes from a plastic perspective.
- Not as well adopted among plastic extrusion companies. It has limited overall adoption, with relatively few logos, especially among plastic extrusion company logos.
- Limited global consolidation capabilities​. You will also have very limited global consolidation capabilities. Therefore, if your company operates in multiple countries and values operational supply chain synergies and collaboration, SYSPRO might not be the best option.
8. QAD
QAD is ideal for companies dealing with highly commoditized products that heavily rely on their supply chain. One of the key strengths of QAD is its integrated solution, which combines both the supply chain suite and ERP within a single platform. This integration is crucial because many other products require separate systems for components like PLM, CAD, ERP, and supply chain management, including WMS and TMS. Plastic extrusion companies, where products are generally commoditized and supply chain planning is essential, tight integration of these components is invaluable. The busy and complex nature of their warehouses necessitates seamless coordination between WMS, TMS, ERP, PLM, CAD, and other processes, making QAD an excellent fit by offering everything from one vendor in a unified solution, eliminating the need to manage multiple systems and ensuring smooth operations. Thus, QAD has secured #8 on our list of top plastic extrusion ERP systems.
Strengths
- Supply chain suite + ERP as part of the suite. The solution integrates the supply chain suite and ERP into one system. It is beneficial for plastic extrusion companies with commoditized products. These companies require effective supply chain planning, as well as WMS and TMS capabilities due to their busy warehouses. QAD fits well because it offers all these components—WMS, TMS, ERP, PLM, CAD—within one solution from a single vendor, avoiding the challenges of managing multiple systems and ensuring seamless integration.
- Process + discrete. QAD has both discrete and process manufacturing natively built into one solution, just like SYSPRO.
- Global capabilities. If you seek global operational synergies, QAD could be a great choice. It localizes in many countries and maintains a broad consulting presence worldwide.
Weaknesses
- New technology might not be stable or rolled out to all modules.They have announced plans to migrate their product to cloud-native technology, but it may take a few years to stabilize, and not all modules will migrate immediately. Understanding which modules have transitioned and how these changes will affect you is important, as the full cloud version may take several years to implement completely.
- Ecosystem. The ecosystem, including the consulting base, isn’t as extensive as what you’ll find with more generalized products, which is typical for prescriptive solutions.
- Not as well adopted among plastic extrusion companies​. It’s not as widely adopted among plastic extrusion companies as some of the other products we discuss in business.
7. Oracle Cloud ERP
Oracle Cloud ERP is a robust solution that stands out compared to other products like QAD or SYSPRO, which are generally smaller and used by smaller companies. As companies grow and outgrow these smaller products, Oracle Cloud ERP becomes a more suitable option. Usually, publicly traded companies use Oracle and they operate with diverse business models that require comprehensive solutions for global financial traceability, along with operational and supply chain traceability when needed. Oracle Cloud ERP is a large-scale product and designed to meet the complex needs of these larger enterprises. Therefore, Oracle Cloud ERP has secured #7 spot on our list of top plastic extrusion ERP systems.
Strengths
- Diversity of the solution supported different business models. Publicly traded companies often have various business models they need to accommodate within a single solution. They prioritize end-to-end global financial traceability, and sometimes operational and supply chain traceability as well, depending on their consolidation needs and the level of traceability they require. In that case, Oracle Cloud ERP will be a great fit.
- Depth of ERP layers for large enterprises. Oracle Cloud ERP provide a better fit for large companies. Its strength lies in its ability to support diverse business models. However, this broad functionality can also be a drawback, as it lacks specialized industry capabilities and integrated suite functions, which can make implementation more costly. The extensive ERP features offer great flexibility for various business transactions, but this complexity often results in longer, more expensive implementations due to the need for thorough testing, configuration, and industry-specific adjustments.
- Global financial consolidation and localization. Global financial consolidation and localization features are crucial, especially in regions like South America and Europe where some products have minimal market presence. These areas can be challenging due to their smaller market share, leading many companies to avoid them due to high R&D costs for localization. In such cases, more generalized products like Oracle Cloud ERP provide a better fit.
Weaknesses
- Limited plastic centric capabilities natively built. The plastic-centric suite capabilities are not as natively developed or supported by the same vendor.
- Expensive implementation. The ERP implementation will be on the expensive side as you are dealing with multiple ERP vendors.
- Not as well adopted among SMB plastic extrusion companies​. SMB plastic extrusion companies do not widely adopt it. Large firms might use Oracle Cloud ERP for its strong financial features, but it may not be the best fit if they need comprehensive operational consolidation in a single solution.
6. SAP S/4 HANA
SAP S/4 HANA is quite similar to Oracle Cloud ERP in many ways. However, SAP S/4HANA tends to be more prevalent in product-centric industries. Its HANA database is slightly superior, particularly for transactional integrity and business models focused on transactions. For product-centric companies that require end-to-end supply chain collaboration across multiple countries and need to consolidate all MRP workflows, SAP S/4HANA is often a better fit. This is especially true when dealing with tightly correlated products or serial numbers, which can increase the overall system workload. Therefore, SAP S/4 HANA secures the #6 spot on our list of top plastic extrusion ERP systems.
Strengths
- ERP layers for complex organizations. Designed for global, highly regulated organizations with very complex business models ranging from discrete to process.
- Process + discrete. Both process and discrete manufacturing are integrated into SAP S/4 HANA. These features are natively built into the solution.
- Global compliance and localization​. Supports localization and compliance requirements of most countries across the world, for companies aiming to consolidate all of their global entities in one database and data model.
Weaknesses
- Limited plastic centric capabilities natively built. Just like Oracle Cloud ERP, the plastic-centric suite capabilities are not as natively developed or supported by the same vendor.
- Expensive implementation. The implementation may be slightly more expensive because you’re dealing with many different vendors and many different add-ons.
- Requires mature internal IT team. In tailoring, customizing, and configuring these capabilities, the same capabilities that are already included as part of the suite, SAP S/4 HANA also requires a very mature internal IT team.
5. Epicor Kinetic
Epicor Kinetic is better suited for plastic extrusion companies that are more discrete in nature rather than process-oriented. These plastic extrusion companies often operate with a hybrid business model. Epicor Kinetic is also ideal for companies that combine manufacturing with distribution. Many plastic companies have a strong presence in e-commerce, and in such cases, they require robust distribution planning and manufacturing-focused solutions. Thus, Epicor Kinetic has secured #5 spot on our list of top plastic extrusion ERP systems.
Strengths
- Complex inventory. The inventory is highly complex, which benefits plastic-centric industries. Generally, this complexity will be reflected throughout your end-to-end processes.
- Formal engineering governance. For industries like aerospace, where you rely heavily on OEMs and need formal engineering processes, or for metal-based manufacturing requiring detailed tracking of attributes, Epicor Kinetic is a great fit. It can handle complex scheduling and planning effectively.
- MES-architecture friendly​. If you need a more MES-centric architecture, where quality and production processes are managed within the MES layer rather than the ERP layer, this can be crucial for industries where production is more critical than end-to-end traceability. In such cases, Epicor Kinetic would be a great fit.
Weaknesses
- Limited plastic-centric capabilities natively built. The plastic-centric capabilities and integration workflows that you can find with IQMS would require add-ons or customization with Epicor Kinetic.
- Weaker suite capabilities for plastic extrusion companies. The suite is not as strong for plastic-centric companies because of missing crucial capabilities for plastic companies.
- Not as well adopted among plastic companies. It’s not as widely adopted among plastic extrusion companies as some of the other products we have discussed in the list.
4. Aptean Process Manufacturing ERP
Aptean Process Manufacturing ERP is well-suited for smaller companies with limited budgets, particularly those seeking a comprehensive suite from a single vendor to simplify implementation. This makes the implementation process generally easier. Compared to other products like Acumatica or Epicor Kinetic, Aptean’s solution is smaller in scale, with fewer layers and less detailed ERP features. In terms of product size, if you were to compare them, Odoo would be the smallest, followed by Acumatica, with Aptean Process Manufacturing ERP falling somewhere in between. Larger systems like Infor CSI and Epicor Kinetic are on the other end of the spectrum. Aptean is ideal for budget-conscious companies. Thus, Aptean Process Manufacturing ERP takes the #4 spot on our list of top plastic extrusion ERP systems.
Strengths
- Full suite pre-integrated. Because a full pre-integrated suite is present, the implementation costs are going to be cheaper.
- Tailored plastic extrusion capabilities. Plastic-extrusion-specific capabilities such as specific PLM, scheduling flows, and quality workflows per customer are natively built with the product.
- Well adopted among process manufacturing companies​. Aptean Process Manufacturing ERP has a much higher penetration among plastic extrusion companies because of cheaper ERP implementation and tailored workflows.
Weaknesses
- Expensive with partial implementation. Buying the complete suite from Aptean may be cheaper. However, if you opt for a rip-and-replace approach or wish to use your favorite tools with Aptean’s solution architecture, costs could increase. You may encounter fewer pre-baked integrations and fewer consultants knowledgeable about these integrations. Aptean may not prioritize supporting external products or suites, which could pose challenges during partial implementations. Thus, choosing between Aptean’s complete architecture or similar products may depend on your specific needs and desired diversity.
- Not as diverse. This is not a good fit for companies with hybrid business models as the data and process model is highly tailored for specific plastic extrusion verticals.
- Some logos but not as well adopted as other plastic-specific capabilities​. Aptean is less widely adopted by plastic extrusion companies than its peers. While they do have some clients in this sector, their presence isn’t as strong as that of other systems on the list.
3. Infor CloudSuite M3
Infor CloudSuite M3 is a much larger product compared to Aptean Process Manufacturing ERP. It is designed for global companies that need to manage global supply chains, operational synergies, collaboration, and consolidation. Infor CloudSuite M3 becomes a better fit when companies outgrow Aptean Process Manufacturing but still require similar capabilities. These companies may have a fixed business model, don’t anticipate significant growth, and are still mindful of budget constraints. Infor CloudSuite M3 offers all these capabilities within a single suite from the same vendor. Therefore, Infor CloudSuite M3 secures #3 spot on our list of top plastic extrusion ERP systems.
Strengths
- Comprehensive process manufacturing capabilities. Process manufacturing capabilities are one of the most robust to support the operations of global process manufacturers with many different business models including retail and rental operations.
- Comprehensive suite supporting most manufacturing processes. Plastic extrusion companies with other business models, such as machinery or food and beverage, would find Infor CloudSuite M3 to be suitable without requiring multiple ERP systems.
- Complex inventory. The inventory is highly complex, which benefits plastic-centric industries. Generally, this complexity will be reflected throughout your end-to-end processes.
Weaknesses
- Not as diverse. This is not a good fit for companies with hybrid business models as the data and process model is highly tailored for specific plastic extrusion verticals.
- Not suitable for SMBs below $250M in revenue. The advanced layers provided as part of the product might be too detailed for smaller companies looking for ERP systems. Thus, posing adoption challenges.
- Ecosystem​. The consulting base and marketplaces are limited for Infor M3 compared to other solutions on this list.
2. Microsoft Dynamics 365 F&O
Microsoft Dynamics 365 F&O is a highly generalized product designed for companies with diverse business models seeking a global presence. It enables these companies to manage all their entities within a single solution, ensuring end-to-end traceability from both financial and operational perspectives. However, because of its broad focus, it doesn’t offer highly tailored capabilities for specific industries. To address this, companies must rely on the partner ecosystem, where vendors provide specialized solutions that are widely adopted alongside the core ERP. Therefore, MS Dynamics 365 F&O secures the #2 spot on our list of top plastic extrusion ERP systems.
Strengths
- Comprehensive localization across the globe. It supports a wide range of business models and offers global localization in areas where other products may not be available, with strong consulting and localization support.
- Ecosystem. Their ecosystem has many options available for plastic-extrusion manufacturers if they want different options if one of the add-ons doesn’t work while having access to a diverse ERP supporting multiple business models.
- The recipe and formulation are supported natively​. The product data model has native support for both process and discrete manufacturing modes.
Weaknesses
- Last-mile plastic extrusion capabilities through third-party vendors. It is ideal for regions lacking other solutions, providing native localization and expert consulting for local taxation, regulations, and processes.
- Expensive implementation. The ERP implementation may be slightly more expensive because you’re dealing with many different vendors and many different add-ons.
- Requires a mature internal IT team. In tailoring, customizing, and configuring these capabilities, the same capabilities that are already included as part of the suite, MS Dynamics F&O also requires a very mature internal IT team.
1. DELMIAWorks
DELMIAWorks (formerly known as IQMS) tops our list because it is the go-to solution for SMB plastic extrusion companies. It remains the most widely adopted product in this sector, even if some companies are still using legacy technology or older versions. These companies value the solution because it incorporates plastic-centric processes, making scheduling, inventory management, and supply chain planning feel seamless and natural. This deep alignment with industry needs is why DELMIAWorks is so highly regarded among plastic extrusion companies. Therefore, DELMIAWorks secures the #1 spot on our list of top plastic extrusion ERP systems.
Strengths
- Most adopted among plastic extrusion companies. IQMS has one of the highest penetrations among SMB plastic extrusion companies because of its tailored workflows and integration.
- Tailored advanced plastic capabilities. The specific plastic-centric capabilities, such as customer-specific quality specifications and unique scheduling requirements with constraints and bottlenecks, are already supported as part of the solution.
- Tailored pre-integrated suite for plastic companies.The plastic-extrusion-specific PLM and supply chain planning add-ons are pre-integrated and managed by the same vendor.
Weaknesses
- Legacy technology. The system technology is very legacy compared to other systems that we have on this list.
- Not as scalable for diverse business models. It may not be as scalable for different business models but is particularly strong for plastic-centric business models. This can also be beneficial for machinery manufacturers who produce their own molds, as they sometimes have plastic components.
- Limited ecosystem and consulting base​. Their ecosystem and consulting base are likely to be limited, as is common with other niche products.
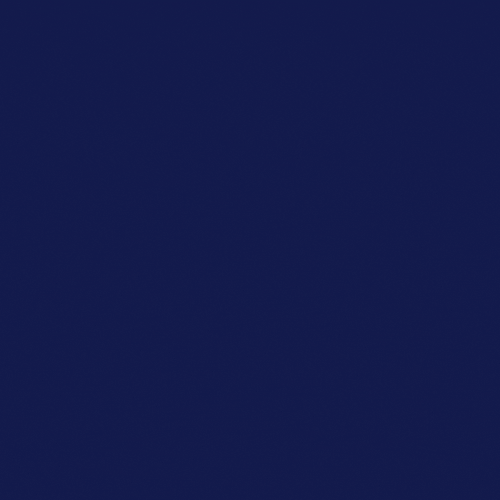
Conclusion
In conclusion, selecting the right ERP system for plastic extrusion companies is crucial for optimizing operations, enhancing efficiency, and meeting industry-specific needs. Each of the top systems reviewed, from DELMIAWorks, which excels in plastic-centric functionalities, to Microsoft Dynamics 365 F&O, known for its diverse business model support, offers unique strengths tailored to different operational scales and complexities. Companies must consider their specific requirements, including inventory management, production capabilities, and the integration of supply chain processes when choosing an ERP solution. While this list offers valuable insights, seeking advice from an independent ERP consultant can greatly enhance your implementation success.