Top 10 EAM Systems In 2024
Similar to other horizontally overlapping categories transcending industries, the Enterprise Asset Management (EAM) category is broad, covering a range of solutions, some integrated with hardware vendors while others deeply buried inside ERP systems. The range of use cases might differ based on the industries – and the asset types tracked. For example, in real estate industries, non-profit, or public sector, the assets include buildings requiring compliance with buildings (and city codes). Other industries, such as food and logistics, might have their own fleets – and integrate with vehicle manufacturers. Yet another industry could be large equipment manufacturing, requiring integration with OEM manufacturers and their processes – making the EAM category especially challenging.
In terms of the solution size, the smaller solutions might be highly prescriptive – and relevant for point use cases. Prioritizing ease of use for smaller organizations, their data models might not be as coded as with larger solutions, making them easier to use – but increasing risks of data integrity. The larger solutions, on the other hand, might be too verbose, covering use cases from many different industries and asset types, making them complex – yet increasing implementation and training time.
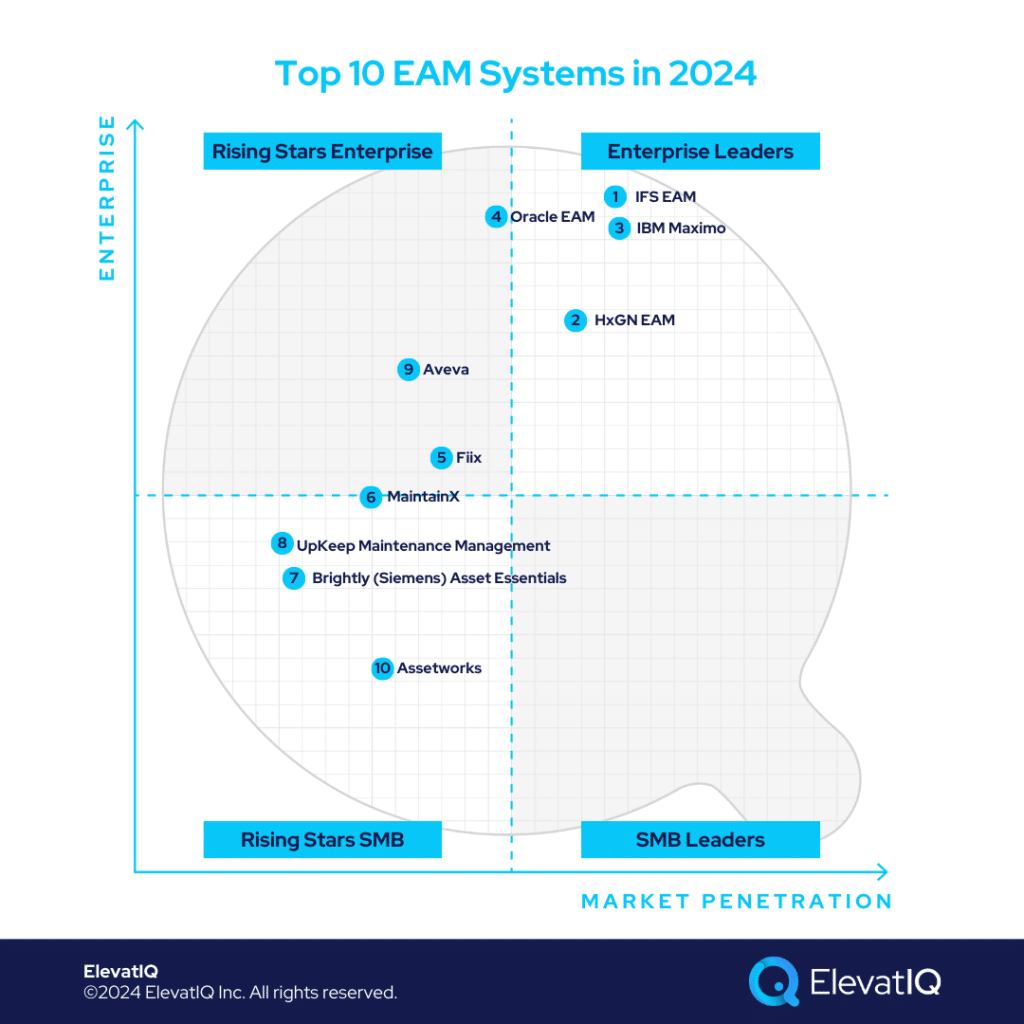
The overlap with other solution categories is another layer that differentiates these solutions. The solutions tightly intertwined with ERP layers might be friendlier for industries where cost tracking of assets and inventory is critical. The other overlap of EAM systems is with CAD, MES, and engineering systems. This is highly relevant for engineering-heavy manufacturing industries. The final overlap could also be with CRM-centric systems, especially the field service and after-market companies. This makes the EAM category extremely nuanced, making it highly challenging for buyers. Don’t panic – and dive into this list to have a basic understanding of these layers.
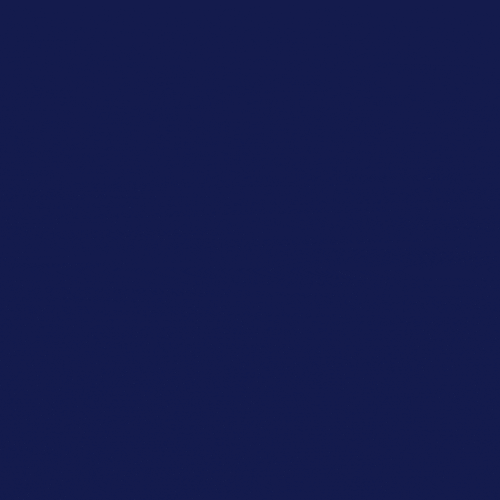
Criteria
- Definition of an EAM system. The companies in this market segment would include companies of all sizes needing an EAM system as a pure-play category that can be deployed without requiring other dependencies.
- Overall market share/# of customers. The higher market share among EAM companies drives higher rankings on this list.
- Ownership/funding. The superior financial position of the EAM vendor leads to higher rankings on this list.
- Quality of development. How modern is the tech stack? How aggressively is the EAM vendor pushing cloud-native functionality for this product? Is the roadmap officially announced? Or uncertain?
- Community/Ecosystem. How vibrant is the community? Social media groups? In-person user groups? Forums?
- Depth of native functionality. Last-mile functionality for specific industries natively built into the product?
- Quality of publicly available product documentation. How well-documented is the product? Is the documentation available publicly? How updated is the demo content available on YouTube?
- Product share and documented commitment. Is the product share reported separately in financial statements if the EAM vendor is public?
- Ability to natively support diversified business models. How diverse is the product in supporting multiple business models in the same product?
- Acquisition strategy aligned with the product: Any recent acquisitions to fill a specific hole for EAM industries? Any official announcements to integrate recently acquired capabilities?
- User Reviews: How specific are the reviews about this product’s capabilities? How recent and frequent are the reviews?
- Must be a best-of-breed EAM product: Only products that can be deployed independently without requiring other dependencies such as ERP, CRM, CAD, or MES.
10. Assetworks
Assetworks is ideal for companies seeking a smaller solution in North America with traceability and maintenance requirements of buildings and fleets. Despite supporting diverse asset types compared to smaller solutions, it might not be the best for large, global companies seeking a centralized solution covering many geographic areas and layers with asset types, which would be available with more enterprise-grade solutions such as IFS or IBM Maximo. They might also not be suitable for companies where inventory and cost tracking is a higher priority than mobile and user experience, securing its place at #10 spot on our list of top EAM systems.Â
Strengths
- SMB-friendly. Assetworks offers a more affordable implementation and is well-suited for small to medium-sized businesses.
- Can cover both properties and fleets. It can manage both properties and fleets. Typically, the workflows for facilities and fleets differ significantly because fleet management systems often have deep integrations with OEMs, while building-centric solutions might require integration with cities and emergency communication systems.
- Polling features​. It supports polling features, which is helpful for companies requiring real-time monitoring and predictive maintenance.
Weaknesses
- Limited to a few geographies. One limitation you may encounter with Assetworks is its restricted coverage in certain regions. If your operations span multiple locations, it may not support all of them.Â
- It is not as cross-functionally integrated as adding inventory manually. Handling inventory costing or serialization scenarios would be a challenge because of text-based inventory on its business objects and form.
- Enterprise search for complex scenarios like inventory items​. Typically, enterprise search requires inventory items to be coded. If your inventory is text-based, it becomes difficult for the system to support those search capabilities that other more advanced systems offer.
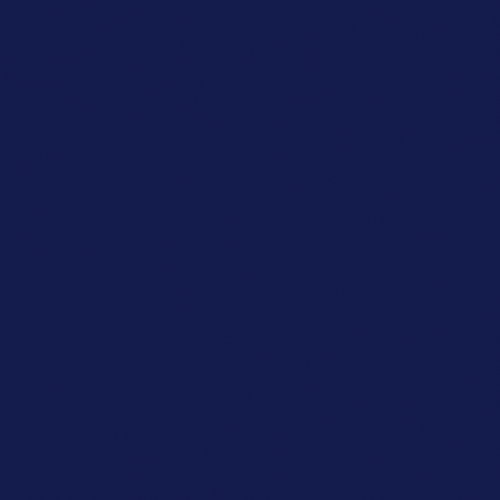
9. Aveva
Aveva is ideal for OT-centric and industry 4.0 industries seeking a pure-play platform – without future expectations of supporting newer business models (or asset types). Providing the integration with hardware vendors, it’s an ideal fit for companies caring for tight embeddedness in their engineering and MES workflows embedded within the same suite. This architecture generally disconnects the operational and financial aspects but might be beneficial for companies prioritizing their plant operations over the needs of other departments at the corporate level, making its name at #9 spot on our list of top EAM systems.
Strengths
- OT-friendly. Aveva is OT-friendly compared to other platforms on this list, supporting the relevant machine and edge integrations required in this industry compared to other platforms on this list.
- MES and engineering workflows are part of the suite. Organizations prioritizing the embeddedness of EAM workflows with engineering and MES would find Aveva attractive.
- Global footprint​. Compared to smaller point solutions such as AssetWorks, Aveva can support relatively global organizations.
Weaknesses
- Legacy UI. The technology is outdated and clunky, so the user interface won’t be as modern as that of other platforms.
- Might not be fit for every industry. It may not be suitable for every industry as it’s primarily an industry-specific solution covering assets and integration relevant to equipment manufacturers and industry 4.0 industries.
- It is not as easy to learn and implement as other smaller solutions​. It could be more challenging to learn and implement as its layers designed for mid-market organizations might be overwhelming for smaller organizations.
8. UpKeep Maintenance Management
Similar to smaller-sized systems such as Assetworks, UpKeep maintenance management is a smaller point solution relevant for SMBs seeing a cloud-native, easier-to-use, and mobile-friendly solution. But these benefits come with compromises, which would be relevant for slightly larger organizations caring for slightly more detailed transactions and data integrity. It might not also be relevant for companies seeking global and diverse asset types, securing its spot at #8 spot on our list of top EAM systems.
Strengths
- SMB-friendly. SMB companies that are limited in budget and technical skill sets would find it relatively easier to implement and use.
Affordable. The solution targets smaller companies and does not layer for mid-sized and enterprise companies, making it super affordable and lightweight for the smaller customer segment it serves. - Mobile-friendly​. Since the underlying technology is cloud-native and the data models are not as connected to prioritize user experience, the solution will be user-friendly compared to other larger solutions.
Weaknesses
- Limited asset and location hierarchies. This would be a challenge for companies maintaining complex asset types and locations where hierarchies would be critical.
- Glitches reported by users. Some users have reported experiencing glitches with the system. With smaller systems that may not be as well-funded, you might encounter similar issues.
- Scalability issues with complex scenarios such as re-occurring work orders​. Intricate billing scenarios and subscription billing might be challenging to manage with this solution.
7. Brightly (Siemens) Asset Essentials
Brightly Asset Essentials, now owned by Siemens, would primarily be software for companies using Siemens machines without the need for additional workflows or an appetite for other software. Due to Siemens’ focus primarily on selling their machines, and this being an add-on feature, it might not receive the same amount of R&D (or attention) as software providers whose core business is to sell software. Also, the competing machine providers would not be as integrated with their software because the goal of the software is to have vendor lock-in. If you are looking for an agnostic option covering more than what this offers, this might not be the best option. But if you can’t afford another software (or have limited use cases just to track and maintain Siemens machines), this would be a great option, securing its spot at #7 on our list of top EAM systems.
Strengths
- SMB-friendly. Primarily a very similar software as AssetWorks for Siemens to differentiate with other machines and have control over their customer’s installations.
- Ease of use. Just like AssetWorks or UpKeep, this would be fairly easy to use due to limited process and data layers, with the primary use being Siemens able to control and report about their machines.
- Cheaper implementation​. Since the data and process layers are relatively simpler and machines are limited to Siemens, the implementation is likely to be super lean.
Weaknesses
- Limited reporting. Substantially limited reporting with the use cases limited to what matters to Siemens.
- Limited scalability for enterprise use cases and asset types​. You will face limited scalability for enterprise use cases if you’re searching for a true enterprise asset management platform that can effectively manage technician workflows and preventive maintenance across various asset types. This may not be the most suitable option.
6. MaintainX
MaintainX is comparable to UpKeep Maintenance and Assetworks, but it is slightly larger and more mid-market friendly than Assetworks. From a technology standpoint, it is cloud-native, mobile-friendly, and offers more layers than Assetworks. Its key strengths are that it’s mid-market friendly, easy to learn and configure, and designed with mobile accessibility in mind. Hence, MaintainX secures the #6 spot on our list of top EAM systems.Â
Strengths
- Mid-market friendly. It is designed specifically for mid-market businesses, offering features that cater to their unique needs.Â
- Easy to learn and configure. MaintainX boasts a user-friendly interface, making it easy to learn and configure for new users.Â
- Mobile-friendly​. It is designed with mobile accessibility in mind, allowing users to manage assets and maintenance tasks.
Weaknesses
- More suitable for facility management than fleet. Another limitation of MaintainX is that it is better suited for facility management than for fleet management. While it can handle complex facility management scenarios with multiple layers, it may not be the ideal choice for transportation companies with in-house fleets.
- Scalability issues with complex datasets such as nested locations. There are scalability issues with complex data sets, like nested locations, as the layers are generally limited. Overall, this product is not designed for enterprise use. It is focused on the mid-market segment, resulting in those limitations.
- Limited security layers. Due to its focus on mid-market, it doesn’t support as detailed security layers as required by enterprises.
5. Fiix
Fiix is also a mid-market-friendly system, with MaintainX being a suitable comparison. It is a cloud-native, mobile-friendly platform that is easy to learn and configure, offering a user-friendly experience similar to MaintainX. In terms of size, it’s larger than smaller systems such as AssetWorks or UpKeep maintenance but smaller than other enterprise-grade systems that may have many detailed security and data layers, securing its spot at #5 on our list of top EAM systems.
Strengths
- Mid-market friendly. It is designed specifically for mid-market businesses, offering features that cater to their unique needs.Â
- Easy to learn and configure. Fiix boasts a user-friendly interface, making it easy to learn and configure for new users.Â
- Mobile-friendly​. It is designed with mobile accessibility in mind, allowing users to manage assets and maintenance tasks.
Weaknesses
- Limited auditability and controls on work orders. The workflow controls for companies seeking audibility, especially around asset availability or inventory, are likely to be limited, causing issues for companies that care for tighter scheduling and costing processes – along with the collaboration aspect of the system.
- Limited scalability for enterprise use cases and asset types. There is limited scalability for enterprise use cases and asset types, which means it may not support all the hierarchies found in systems like IFS or IBM Maximo. These systems offer richer asset types with more detailed hierarchies (and use cases) to accommodate enterprise-grade scenarios.
- Data integrity issues are caused by the loose data model​. The data model is not as coded as the larger peers – as the system prioritizes user experience over data integrity and control. So, you are likely to have data integrity issues, requiring manual maintenance and governance.
4. Oracle EAMÂ
Oracle EAM is an enterprise-grade asset management product particularly suited for companies using Oracle Cloud ERP. Offering more advanced data models compared to smaller SMB-focused systems, it handles complex asset hierarchies and diverse asset types. However, it lacks the pre-built integrations often found in smaller solutions, leading to a more challenging and resource-intensive implementation. The learning curve is steeper, and using the system generally requires more internal and external expertise, making it harder to use overall. Therefore, Oracle EAM secures the #4 spot on our list of top EAM systems.
Strengths
- Enterprise-grade capabilities. From a data model perspective, this products offer much more, but they may lack the numerous pre-built integrations found in smaller systems targeting the SMB sector.Â
- Predictive maintenance based on real-time sensor data analytics. Predictive maintenance relies on real-time sensor data analytics, which is included in the Oracle EAM portfolio. However, implementing these capabilities will require significant consulting support.
- Supports complex assets to support reliability analysis​. Supporting complex assets for reliability is essential, especially in sectors like IT, media, and telecom. When aiming to meet reliability metrics and SLAs, particularly when managing customer assets.
Weaknesses
- Expensive. Oracle EAM will be expensive from the implementation perspective as it requires a lot of consulting help.Â
- Steep learning curve. The learning curve will be steeper, as is typical with enterprise products, and you will likely need extensive customization during the implementation process.
- Might require add-ons for integrated capabilities​. The integrated capabilities that might be available with smaller systems might be vanilla with larger systems – as they serve a diverse set of industries, missing specific capabilities for micro-verticals (and asset types).
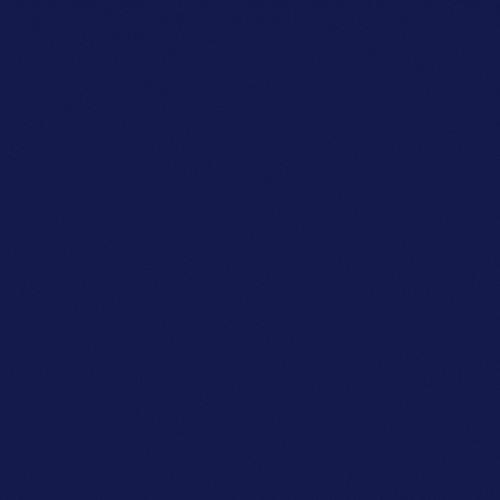
3. IBM Maximo
IBM Maximo is one of the most widely adopted asset management products, particularly for enterprises, excelling in sectors like public services and non-profits. Its key strength lies in its deep enterprise-grade capabilities to handle complex scenarios, hierarchies, and diverse asset types. Architecturally, it’s similar to Oracle EAM, offering strong data and process models but lacking pre-built integrations. Like Oracle EAM, Maximo can be difficult to use, requiring extensive training, change management, and a significant investment in implementation. However, its high customizability allows for extensive support of unique data models and processes. Therefore, IBM Maximo has secured the #3 spot on our list of top EAM systems.Â
Strengths
- Enterprise-grade capabilities. It possesses robust enterprise-grade capabilities designed to handle all of those complex scenarios.
- Hierarchies and attributes. From the IBM Maximo perspective, hierarchies and attributes are crucial, as each asset may require tracking thousands of attributes for effective reporting and planning.Â
- Complex scheduling rules and workflows. Complex scheduling rules and workflows are necessary when managing numerous assets for both yourself and your clients. In this context, IBM Maximo is likely to be an excellent fit due to its enterprise-grade capabilities.
Weaknesses
- Limited mobile capabilities. They are going to be fairly limited compared to other EAM systems mentioned in this list because of their legacy technology and tight data model.Â
- Steep learning curve. The learning curve will be steeper, as is typical with enterprise products, and you will likely need extensive customization during the implementation process.
- Might require add-on for BIM integration​. The smaller products are likely to support pre-baked integrations, more in the plug-and-play form, because of the fluidity of their data model, which might not be possible with enterprise products such as IBM Maximo.
2. HxGN EAM
HxGN EAM is also an enterprise-grade asset management solution. Previously owned by Infor, Hexagon now maintains a close alignment with existing Infor installations. However, as a machine provider, Hexagon’s primary focus is on selling its machinery, which leads to tighter integration with its asset management product. While HxGN EAM offers slightly more advanced enterprise capabilities, its incentive is to integrate closely with its own assets to drive sales. It is comparable to IBM Maximo and Oracle EAM but is generally more friendly towards OT applications. In contrast, it may not provide as many layers or detailed capabilities for property management or transportation management scenarios. Therefore, HxGN EAM has secure the #2 spot on our list of top EAM systems.Â
Strengths
- Detailed user privileges. The user privileges in HxGN EAM are quite detailed compared to other smaller point solutions.Â
- Ability to support complex asset installations. Like other Infor products, it excels in workflow, security, user-controlled processes, and customization. This makes it particularly useful for managing and supporting complex asset installations.
- Enterprise-grade capabilities to support most asset types​. If you’re a manufacturer with a wide variety of assets to track and maintain, HxGN EAM could be an excellent fit. Similar to IBM Maximo, it offers enterprise-grade capabilities to support various asset types, making it a strong choice for enterprise environments.
Weaknesses
- Legacy UI. The limitations of HxGN EAM are similar to IBM Maximo, particularly with its legacy user interface, as it’s built on older technology. While IBM Maximo has made some advancements in cloud and data technology, making it slightly faster, HxGN EAM still operates with a more dated UI.
- Limited mobile capabilities. The legacy technology and tight data model prevent the same fluid experience that is generally found with smaller systems.
- Poorly documented​. Users report the software is not as well documented, requiring consulting help with ongoing maintenance and support.
1. IFS EAM
IFS EAM is an enterprise-grade asset management solution that is widely adopted in industries such as MRO, airlines, oil and gas, and telecom. With their workflows closely integrated with field service operations, these sectors typically require complex scheduling and management of intricate assets. A significant advantage of IFS is its two best-of-breed enterprise-grade products, field service management, and enterprise asset management, which work seamlessly together for these industries. Compared to other enterprise-grade solutions like IBM Maximo or Hexagon EAM, IFS offers superior technology, making it somewhat easier to use. Therefore, IFS has secured the #1 spot on our list of top EAM systems.
Strengths
- Ease of use. When compared to other enterprise-grade products like IBM Maximo and Hexagon EAM, IFS technology stands out as superior.
- Enterprise-grade capabilities. IFS EAM features an underlying data model that supports enterprise-grade scenarios, encompassing capabilities, customization, and workflow security. All these functionalities are integral to the IFS EAM system.
- Strong predictive maintenance and facility maintenance capabilities​.
Weaknesses
- Limited language packs. The language packs are not as comprehensive as enterprise companies would expect for global deployments.
- It would require consulting help. Since the product is highly complex and designed for enterprise use cases – with thousands of layers of dependencies within their data model, it requires substantial consulting help with implementation (and ongoing upkeep of the system).
- Expensive​. SMBs not caring for enterprise layers might feel that the product is relatively more expensive than other smaller point solutions.
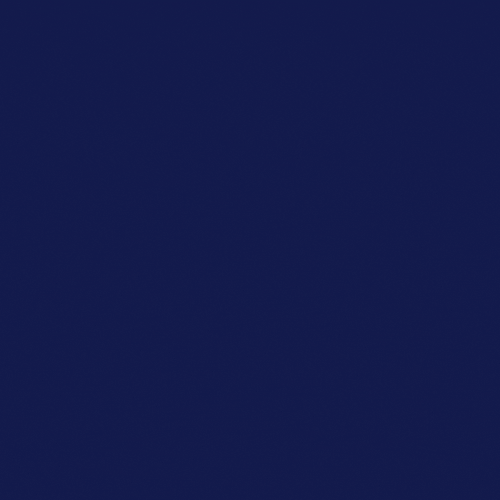
Conclusion
In summary, choosing the right EAM system is a complex decision influenced by various factors, including industry needs, company size, and the specific asset types involved. This list highlights the strengths and weaknesses of the top EAM systems, ranging from SMB-friendly, budget-conscious options to enterprise-grade solutions with advanced capabilities for larger organizations. Whether a company prioritizes mobile accessibility, ease of integration, or highly detailed functionality, each solution has unique advantages and limitations that make it suitable for specific applications. By understanding the nuances of each EAM system, buyers can make informed choices aligned with their asset management goals. While this list offers valuable insights, seeking advice from an independent ERP consultant can greatly enhance the implementation success.